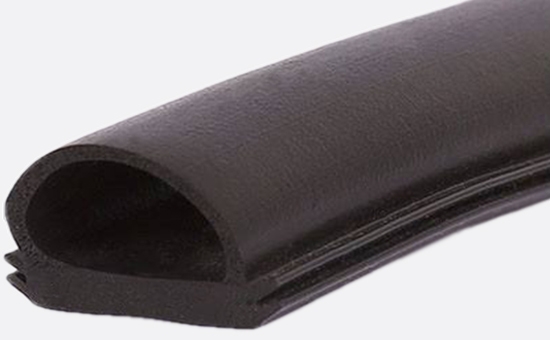
PP is a polymer formed by the addition polymerization of polypropylene and propylene. It has excellent chemical resistance, heat resistance, electrical insulation, high mechanical strength, and good processing performance. It is combined with a suitable amount of EPDM or EPDM. The blending of acrylic reclaimed rubber can further improve the impact performance and low temperature brittleness of PP materials. But in actual production, the addition of EPDM compound will cause the scratch resistance of pp material to decrease. What should I do at this time?
1. Use high wear-resistant filler
When using EPDM rubber to improve the overall performance of PP materials, reasonable use of high wear-resistant fillers can improve the wear resistance and scratch resistance of the blended materials. For example, transition metal oxide molybdenum dioxide with high conductivity, high melting point and high chemical stability, graphite with a unique lattice structure, glass fiber, carbon fiber, and aramid fiber.
The unique lattice structure of graphite allows graphite molecules to slide easily with each other when subjected to a small frictional force, which is an ideal wear-resistant additive.
Glass fiber has high temperature resistance and high tensile strength, improves the structural integrity of thermoplastics while improving wear resistance, and improves the wear resistance, load resistance, thermal conductivity and thermal deformation of PP/EPDM blends. Carbon fiber 2LLYY109 has the characteristics of high temperature resistance, friction resistance, electrical conductivity, heat conduction and corrosion resistance, soft texture, low scratch resistance, and can significantly improve the integrity, load resistance and wear resistance of the pp blend material structure. Aramid fiber is the softest and least scratch-free fiber material.
2. Use wear-resistant processing aids
The use of wear-resistant processing aids in the preparation of PP/EPDM blends can also improve the scratch resistance of the blends to a certain extent. PTFE has good lubricity and wear resistance under friction. Liquid polysiloxane as a wear-resistant additive in thermoplastic elastomers will slowly migrate to the surface of the elastomer and form a continuous film, thereby improving the scratch resistance of PP/EPDM blends. Low-viscosity silicone is easy to volatilize . Adding an appropriate amount of slip agents such as oleic acid amide, erucamide, etc. to the PP/EPDM blend material can produce a wax layer on the surface of the blend material to reduce the friction coefficient and reduce the visibility of scratches.
Rubber and plastic blends are more and more widely used in various industries. Improving the scratch resistance of PP/EPDM blends is of great significance to expand the scope of use of PP/EPDM thermoplastic elastomers. According to actual needs, appropriate measures can be taken to meet different rubber and plastic products. Performance requirements.
Exclusive original article [commercial authorization] reprint, excerpt and excerpt in any form are prohibited without written authorization. Focus on Hongyun rubber: learn the process formula and raw material technology of producing rubber products from recycled rubber to help you reduce costs and increase profits