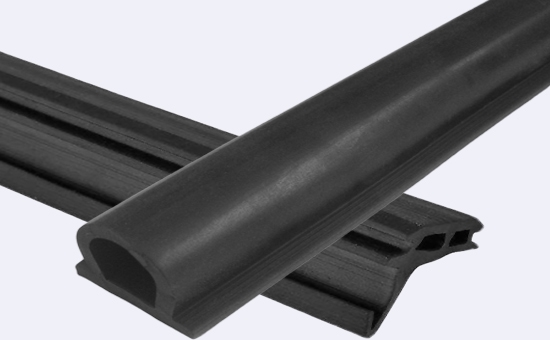
EPDM rubber has excellent high temperature resistance, weather resistance, ozone resistance, chemical resistance, etc., and is widely used in the production of various rubber sealing strips. When using EPDM rubber to produce extruded sealing strips, the quality of the semi-finished rubber compound directly affects the performance and service life of the finished sealing strip. In actual production, rubber product manufacturers need to select the appropriate mixing process according to the processing characteristics of the EPDM compound to further improve the comprehensive performance of the EPDM extrusion sealing strip.
1. Choose the skill of mixing with open mixer
The main chain of EPDM rubber is composed of chemically stable saturated hydrocarbons. The EPDM rubber molecules after simple mastication usually cannot be broken or degraded, and the rollability cannot be obtained. The Mooney viscosity value must reach a certain range.
When the EPDM extruded sealing strip compound is mixed with an open mixer, the roll pitch of the thin pass should be adjusted to a small roll pitch of 0.2-1mm, and the thin pass should be 5-10 times at room temperature; the temperature of the roll before mixing 2LLYY923 is controlled at 40 Between -70℃, the temperature of the rear roll is controlled at 50-80℃; the dripping method is selected for oil filling; when mixing EPDM rubber with high Mooney or higher diene content, the mixing temperature can be appropriately increased. The mixing time is appropriately extended.
2. Choose the mixing skills of internal mixer
EPDM rubber has the characteristics of high-temperature thermoplasticity. It is tanned under high temperature conditions. The compound and oil are easy to disperse and the mixing uniformity is good. Compared with the open mixer, the EPDM is mixed with an internal mixer. Rubber usually can obtain good mixing effect in a short time under high temperature conditions.
Generally, the EPDM rubber with high Mooney viscosity is mixed with an internal mixer when producing extruded sealing strips. The mixing temperature of EPDM sealant rubber compound is higher than that of other rubbers. It can be controlled at about 160℃. Good mixing effect can be obtained after mixing for 4-5 minutes. Extruded rubber materials are mostly mixed in two stages. After mixing EPDM rubber, fillers, reinforcing agents, softeners, etc., the vulcanization system is added in the second stage.
In order to reduce production costs and improve economic benefits, many rubber product manufacturers choose to use EPDM rubber seals in appropriate amounts. The processing performance of EPDM reclaimed rubber is somewhat different from that of EPDM virgin rubber, and its plasticity is higher. Generally, EPDM rubber is fully plasticized and then mixed with reclaimed rubber, and internal mixers are often used for mixing. . In order to make the excess gas in the rubber compound separate out and the compounding ingredients are fully and evenly mixed, the rubber compound needs to be parked and cooled. The extruded rubber material has good stiffness and compactness to ensure the smooth extrusion and vulcanization of the extruded sealing strip and the sealing strip is not easily deformed .
Exclusive original article [commercial authorization] reprint, excerpt and excerpt in any form are prohibited without written authorization. Focus on Hongyun rubber: learn the process formula and raw material technology of producing rubber products from recycled rubber to help you reduce costs and increase profits