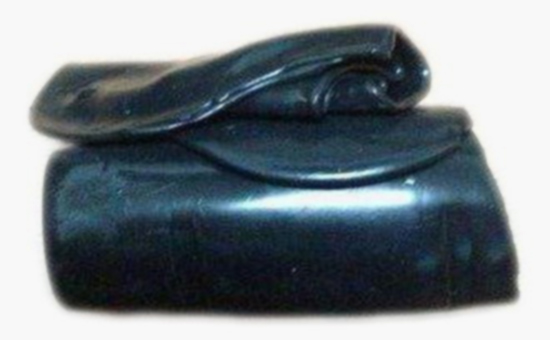
In order to ensure that the rubber compound is evenly dispersed during mixing, the rubber compounding process containing the reclaimed rubber is mostly carried out in an internal mixer. The rubber products with the EPDM reclaimed rubber as the main raw material are also mainly densely mixed, but In actual production, there may be problems of poor dispersion when EPDM reclaimed rubber is mixed. Why is this? Where should we consider the solution?
1. EPDM reclaimed rubber and original rubber are improperly selected
EPDM reclaimed rubber + EPDM rubber is a commonly used processing method for EPDM rubber products processing enterprises. If the selected EPDM reclaimed rubber and the original rubber Mooney viscosity are too different, or the reclaimed rubber itself is selected. Mooney is too high, and the high ethylene content of EPDM rubber will lead to poor dispersion of EPDM rubber in the internal mixer; the rubber or impurities of EPDM or reclaimed rubber will also cause uneven mixing. The problem occurred. This requires rubber products processing enterprises to consider a variety of factors when selecting EPDM reclaimed rubber or EPDM rubber, and choose the most suitable rubber type.
2. The formulation of EPDM recycled rubber products is unreasonable
When using EPDM reclaimed rubber to produce high-hardness rubber products, too much hard carbon black or too little liquid softener will cause the rubber to be too dry and agglomerated, resulting in poor dispersion of reclaimed rubber; producing low hardness EPDM Excessive rubber oil in reclaimed rubber products causes the rubber to be "diluted" by oil so that the rubber compound is poorly dispersed, or the use of materials such as high melting point resin in soft EPDM products may cause poor dispersion of the rubber; EPDM The inclusion of impurities in the reclaimed rubber product is also one of the causes of poor dispersion: therefore, the various compounding agents in the formulation of the EPDM reclaimed rubber product must be selected and selected.
I believe that every customer who chooses EPDM reclaimed rubber has a desire to reduce the production cost, but if the cost of the formula is lowered repeatedly in order to reduce the cost (such as adding a large amount of reclaimed rubber with low EPDM content or Is to increase the non-reinforcing filler) will directly lead to the dispersion of EPDM reclaimed rubber/original glue in the internal mixer; on the other hand, if the EPDM rubber content is too high, it will cause poor dispersion. Typical non-self-reinforcing rubber, EPDM is very much needed to be "filled". Therefore, when designing the formulation of EPDM reclaimed rubber products, it is necessary to reasonably determine the gel content of the formula according to the actual demand, and avoid excessively high or low.
Exclusive original article [commercial authorization] reprint, excerpt and excerpt in any form are prohibited without written authorization. Focus on Hongyun rubber: learn the process formula and raw material technology of producing rubber products from recycled rubber to help you reduce costs and increase profits