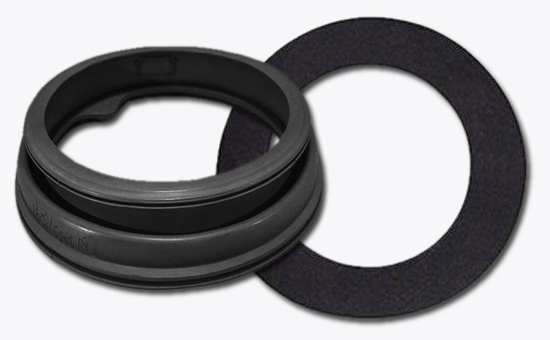
EPDM reclaimed rubber has excellent high and low temperature resistance, weather resistance, ozone resistance, etc., and is widely used in the production of various sealing rings, reducing raw material costs under the premise of ensuring quality. The compatibility of EPDM reclaimed rubber with other types of general rubber is better than that of EPDM virgin rubber. It can be used together with butadiene rubber and styrene butadiene rubber to produce rubber seals with better comprehensive performance. I will share a ternary with you today. The formula of ethylene propylene reclaimed rubber/butadiene rubber/styrene butadiene rubber is used for production of sealing ring, for reference only.
70 parts of EPDM reclaimed rubber, 35 parts of butadiene rubber, 15 parts of styrene butadiene rubber, 6 parts of mercury oxide, 1 part of stearic acid, 8 parts of carbon black, 5 parts of activated calcium carbonate, 4 parts of white carbon black, sulfuric acid 30 parts of barium, 6 parts of diethylene glycol, 15 parts of paraffin oil, 2.5 parts of cashew nut shell liquid, 6 parts of TOTM, 8 parts of white ointment, 2 parts of paraffin, 1.5 parts of antioxidant, 10 parts of zinc borate, 10 parts of titanium dioxide, 2.5 parts of sulfur, 1.5 parts of DCP, 2 parts of accelerator; total: 241 parts.
When using EPDM reclaimed rubber to produce sealing rings, the addition of butadiene rubber and styrene butadiene rubber can further improve the elasticity, cold resistance and wear resistance of the sealing ring; the amount of butadiene rubber 2LLYY1021 can be controlled at 35- according to actual needs. Between 40 parts, the amount of SBR is controlled between 10-15 parts.
1. Significance of combined use of sulfur and peroxide
In actual production, traditional sulfur vulcanizates produce polysulfide bonds. The vulcanizates have high mechanical strength, but they are prone to vulcanization reactions under high temperature conditions. The polysulfide bond energy is small, the stability is poor, and the vulcanizates have poor aging resistance. Good, vulcanizate has large compression deformation. The C-C bond produced by peroxide vulcanization has high bond energy and high stability, but the mechanical strength of the vulcanizate is low. The combined use of sulfur/peroxide for EPDM reclaimed rubber seals can further improve the mechanical strength, heat resistance, and compression set resistance of the finished product.
2. Selection and application of flame retardants
Rubber flame retardants can be divided into additive flame retardants and reactive flame retardants. Additive flame retardants mainly include organic flame retardants and inorganic flame retardants, halogen flame retardants and non-halogen flame retardants. Zinc borate is a typical environmentally friendly non-halogen flame retardant. It has the characteristics of non-toxic, low water solubility, high thermal stability, small particle size, small specific gravity, and good dispersion. It is used in EPDM reclaimed rubber/butadiene rubber/styrene butadiene rubber. The rubber sealing ring can effectively improve the flame retardancy of the product.
3. The role of other compounding agents in EPDM sealing ring
Mercury oxide can further improve the compression set resistance of the finished seal ring in the production of EPDM rubber/butadiene rubber/styrene butadiene rubber seal ring; after using fatty acid to activate and modify calcium carbonate, the surface properties of calcium carbonate can be modified by The water becomes lipophilic and it has better compatibility with rubber to improve the reinforcing effect of calcium carbonate in the vulcanized rubber; barium sulfate can increase the specific gravity of the EPDM seal ring and improve the acid and alkali resistance of the finished seal ring.
Diethylene glycol, TOTM and cashew nut shell liquid can be used as plasticizers, among which cashew nut shell liquid can improve the compatibility between EPDM, butadiene rubber and styrene butadiene rubber, and further improve the flexibility of the sealing ring , Heat resistance, weather resistance and easy drying; TOTM can improve the heat resistance and durability of products.
When using EPDM reclaimed rubber and general synthetic rubber together to produce rubber seals with more stable performance, butadiene rubber, styrene butadiene rubber, and ethylene propylene rubber are ideal choices. In actual production, the combined use ratio of EPDM reclaimed rubber/butadiene rubber/styrene butadiene rubber combined rubber can be determined according to actual needs. Rubber product manufacturers can appropriately increase the amount of EPDM reclaimed rubber and adjust the formula in time to ensure Under the premise of the quality of the sealing ring, more raw material costs are reduced.
Exclusive original article [commercial authorization] reprint, excerpt and excerpt in any form are prohibited without written authorization. Focus on Hongyun rubber: learn the process formula and raw material technology of producing rubber products from recycled rubber to help you reduce costs and increase profits