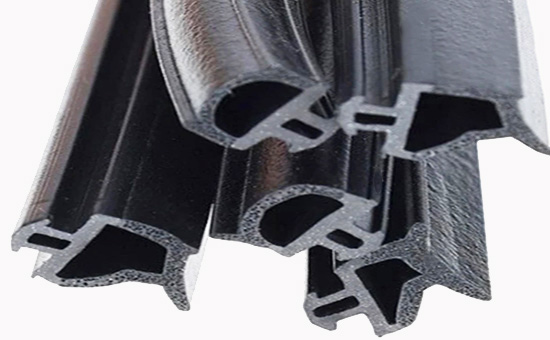
EPDM recycled rubber is made by desulfurization and regeneration of waste EPDM rubber and its products, with excellent high and low temperature resistance, weather resistance, ozone resistance, etc. It can completely or partially replace EPDM rubber in the production of EPDM products, effectively reducing raw material costs. When producing rubber products using EPDM recycled rubber as the main raw material, the mixing process directly affects the finished product. This article mainly shares with you the mixing characteristics of commonly used raw materials in the production of EPDM recycled rubber products.
1. Mixing characteristics of EPDM rubber
EPDM recycled rubber is often used in combination with the original rubber to produce rubber products, reducing costs while ensuring product quality. Compared with recycled rubber, EPDM rubber has poorer wetting properties for fillers and compounding agents, and slower mixing speed; Moderate use of softeners or processing aids to improve its mixing performance. EPDM rubber is more sensitive to temperature when wrapped around the rollers of the open mill; Within the allowable temperature range, increasing the mixing temperature appropriately can promote the rapid and uniform dispersion of fillers.
2. Mixing characteristics of compounding agents for EPDM reclaimed rubber vulcanization system
(1) Sulfur: Sulfur plays a crucial role in the vulcanization process of EPDM reclaimed rubber. Due to its low melting point, liquefaction and agglomeration occur above 100 ℃. Therefore, when adding sulfur, the temperature of the rubber material must be cooled below 100 ℃ to facilitate dispersion. To prevent burning, sulfur is usually added in the final stage of mixing and the operation is required to be completed quickly; If necessary, sulfur can also be pre mixed with EPDM raw rubber to form masterbatch particles for use.
(2) Zinc oxide: Zinc oxide is widely used in the production of EPDM recycled rubber products, including lightweight zinc oxide and active zinc oxide; Among them, active zinc oxide has a better effect on improving the vulcanization rate of E4LYY11 EPDM reclaimed rubber. Zinc oxide is easily mixed into rubber, but it is extremely difficult to disperse. To improve the dispersion effect of zinc oxide during mixing, it is best to use pre granulated zinc oxide particle formulations or directly select finer zinc oxide particles.
(3) Accelerator: Accelerators are mostly powdered substances that require uniform mixing and good dispersion in the rubber compound to avoid affecting the properties of EPDM reclaimed rubber or causing frost spraying; Choosing pre made granulation accelerators can effectively prevent losses caused by powder accelerators flying and improve their dispersibility in EPDM reclaimed rubber. The temperature of the rubber compound when mixing and adding accelerators for EPDM rubber and EPDM reclaimed rubber is generally controlled below 100 ℃. The vulcanization time should be shortened as much as possible while ensuring the uniform dispersion of the compounding agent to avoid burning.
In addition, the EPDM recycled rubber compound with added accelerators needs to be cooled immediately after cutting and used within the specified period of time to avoid failure due to burning.
3. Mixing characteristics of additives in the reinforcement and filling system of EPDM reclaimed rubber
(1) Carbon black: The most commonly used reinforcing agent for EPDM recycled rubber products. The smaller the particle size and the larger the surface area of carbon black, the poorer its wetting properties for EPDM recycled rubber and the more difficult it is to disperse. The amount of carbon black used is large, and adopting a batch feeding method can achieve good dispersibility.
(2) Inorganic fillers: The difficulty of dispersion depends on the particle size. The smaller and more difficult the inorganic filler particles are to disperse, the greater the heat generation, and the better the reinforcement effect; Surface chemical pretreatment of fillers used in the vulcanization formula of EPDM reclaimed rubber before use, or the addition of processing aids such as dispersing agents and flow aids, can improve the dispersibility of the compounding agent.
4. Mixing characteristics of softening and plasticizing system additives for EPDM reclaimed rubber
The role of compounding agents in softening and plasticizing systems is to improve the processing and handling performance of rubber materials, usually in the form of processing oil and operating oil.
Paraffin based, cyclic based, and aromatic based operating oils have better compatibility with ethylene propylene rubber and are used in large quantities in the production of EPDM recycled rubber products. The type of softener has a significant impact on dispersion; Aromatic based oils have the highest dispersion in EPDM rubber compounds, followed by cyclic based oils, and alkyl based oils have the lowest. The use of oil handling agents will reduce the viscosity of the rubber material, which is not conducive to the dispersion of carbon black. Add carbon black first and then add oil separately, and add oil as soon as possible while ensuring dispersion, which can promote the dispersion of carbon black.
The mixing characteristics of EPDM recycled rubber are crucial for producing high-quality rubber products. By optimizing the mixing process and selecting appropriate raw materials and additives, the performance and application range of EPDM reclaimed rubber can be significantly improved.
Exclusive original article [commercial authorization] reprint, excerpt and excerpt in any form are prohibited without written authorization. Focus on Hongyun rubber: learn the process formula and raw material technology of producing rubber products from recycled rubber to help you reduce costs and increase profits