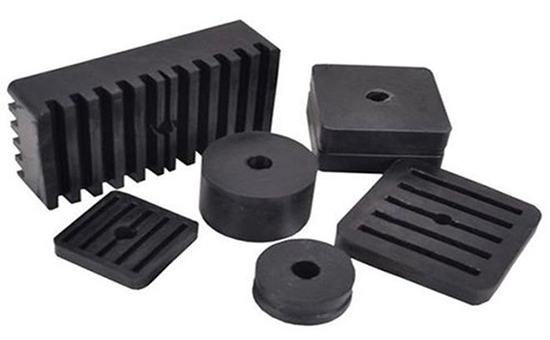
EPDM reclaimed rubber is used to replace EPDM rubber to produce various rubber products such as EPDM hoses, sealing strips, etc., and the vulcanization system is the key factor that determines its physical and mechanical properties and processing performance. In the production of EPDM reclaimed rubber products, it is of great significance to choose the appropriate vulcanization system to improve the performance of reclaimed rubber and reduce costs. In actual production, the commonly used vulcanization systems of EPDM recycled rubber include sulfur vulcanization system, peroxide vulcanization system, resin vulcanization system and quinone oxime vulcanization system.
1. Sulfur vulcanization system
The sulfur vulcanization system is the most commonly used vulcanization method for EPDM reclaimed rubber. The sulfur vulcanization system has the advantages of safe operation, moderate vulcanization rate and excellent physical and mechanical properties. When using EPDM reclaimed rubber E4LYY111 as the main raw material to produce rubber products, the amount of sulfur should be controlled in the range of 1-2 parts to avoid frosting and the decline of heat resistance. The selection and dosage of accelerators have a significant impact on the vulcanization rate and rubber properties, and the commonly used accelerators for EPDM reclaimed rubber products include thiuram and dithiocarbamate.
2. Peroxide vulcanization system
The peroxide vulcanization system is suitable for EPDM rubber products with high requirements for high heat resistance and low compression set, and the commonly used peroxide is cumene peroxide (DCP), and the dosage is generally 2-3 parts. When EPDM reclaimed rubber is vulcanized with peroxide, the vulcanized rubber has good heat resistance and aging resistance. It should be noted that the low temperature vulcanization rate of peroxide vulcanization system is slow and the cost is high.
3. Resin vulcanization system
The resin vulcanization system is suitable for EPDM reclaimed rubber products that require high-temperature thermal stability and low compression set by using reactive alkylphenolic resins and halogen-containing compounds. The disadvantages of the resin vulcanization system are low elongation and high hardness; The vulcanization process requires the addition of halides as catalysts, while also paying attention to the corrosive nature of halides.
4. Quinone oxime vulcanization system
The quinone oxime vulcanization system can provide excellent aging resistance for EPDM reclaimed rubber vulcanized rubber, but the disadvantages of the system are poor physical and mechanical properties, high hardness, and high cost. The dosage ratio of quinone oxime to lead oxide is about 6:10, and the ratio of GMF to S dosage is about 1.0:(0.4-0.8).
In actual production, the vulcanization system of EPDM reclaimed rubber is mainly sulfur vulcanization system and peroxide vulcanization system, and different vulcanization systems have a direct impact on the Mooney viscosity, scorch time, vulcanization rate, cross-linking bond type and physical and mechanical properties (such as stress, strain, hysteresis, compression deformation and heat resistance) of EPDM reclaimed rubber compound. When designing the vulcanization system of EPDM recycled rubber, it is necessary to consider the performance requirements, processing cost and safety of the product. By rationally selecting the vulcanization system and adjusting the dosage of compounding agent, the performance of reclaimed rubber can be optimized to meet the needs of different applications.
Exclusive original article [commercial authorization] reprint, excerpt and excerpt in any form are prohibited without written authorization. Focus on Hongyun rubber: learn the process formula and raw material technology of producing rubber products from recycled rubber to help you reduce costs and increase profits