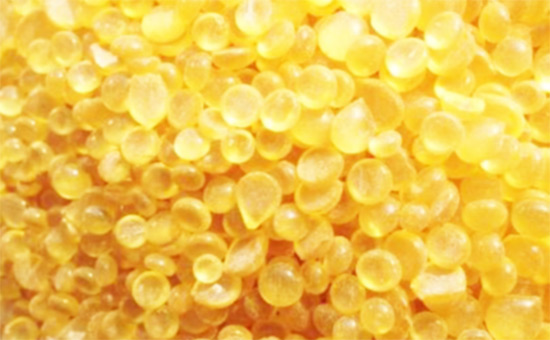
The use of butyl regenerated rubber instead of butyl rubber to produce high-air-tight rubber products, corrosion-resistant products, and shock-absorbing and damping parts can significantly reduce the cost of raw materials while ensuring product quality. There are three kinds of vulcanizing agents commonly used in the production of rubber products using butyl reclaimed rubber: sulfur, diterpenoids and paranitroso compounds, and resins, among which the butyl regenerated rubber products vulcanized with resin vulcanizing agents have excellent high temperature resistance and are available In the production of butyl reclaimed rubber products such as water tires, diaphragms, and curing bladders.
The use of resin cured butyl reclaimed rubber products with excellent high temperature performance is inseparable from the heat-stabilized CC bonds and -COC crosslinks that are generated during the curing process. The stability of these cross-linked bonds for thermal and mechanical applications is indispensable. It is higher than the -CSC-type cross-linking bond, so it can be used for a long time under high temperature conditions to maintain good vulcanization performance. Among them, phenolic resin is the most commonly used vulcanizing agent for butyl regenerated rubber.
Phenolic resin has excellent high temperature performance, structural integrity and dimensional stability, so the butyl regenerated rubber cured with phenolic resin can be used at a temperature of around 160 degrees Celsius to maintain a good low compression set and excellent resistance Aging performance. The octyl phenolic resin and the p-tert-butyl phenolic resin in the phenolic resin are typical representatives of the phenolic resin used in the vulcanization of the butyl regenerated rubber, among which the compatibility between the octyl phenolic resin and the butyl regenerated rubber is good, and after vulcanization The butyl regenerated rubber compound has higher timing stress. Carboxymethyl phenolic resin can also be used as a vulcanizing agent in the curing system of butyl regenerated rubber products.
When butyl regenerated rubber products are vulcanized with phenolic resins, activators are indispensable compounding agents. Among them, metal chlorides (stannic chloride, ferric chloride) and halogen-containing compounds are commonly used as activators in resin vulcanization systems. The use of stannous chloride as an activator makes it difficult to use zinc oxide, otherwise it will delay the curing; the halogen-containing polymer is just the opposite, and the addition of zinc oxide can accelerate the curing process of the butyl regenerated rubber product.
Phenolic resin is not only important in the production of butyl regenerated rubber products, but also can be used in the production of other types of rubber products as vulcanizing agents, reinforcing agents or modifiers, such as adding phenolic resin to nitrile rubber. Resin as a reinforcing agent can improve the tensile strength, tear strength, hardness and other indexes of nitrile vulcanizate, and improve the heat resistance, flex resistance, and chemical corrosion resistance of nitrile rubber products. It can be seen that phenolic resin has an extremely wide range of applications in the field of rubber products. With regard to the use of phenolic resins for curing butyl regenerated rubber, there are many other issues that you and I will jointly discover and discuss.
Exclusive original article [commercial authorization] reprint, excerpt and excerpt in any form are prohibited without written authorization. Focus on Hongyun rubber: learn the process formula and raw material technology of producing rubber products from recycled rubber to help you reduce costs and increase profits