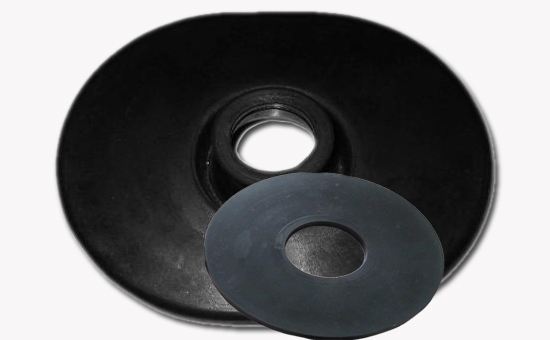
EPDM rubber has excellent heat resistance, weather resistance, and aging resistance. The preparation of various shock-absorbing materials has excellent dynamic performance, good damping performance, and shock-absorbing products have good performance and long life. EPDM reclaimed rubber retains the basic performance characteristics of EPDM rubber, is resistant to high and low temperatures, and is resistant to aging. It can completely or partially replace EPDM raw rubber to prepare shock-absorbing materials, effectively reducing raw material costs and saving industrial and electrical costs.
1. Use scene of EPDM reclaimed rubber shock absorption material
EPDM rubber compound containing EPDM reclaimed rubber can be used to prepare shock-absorbing rubber products such as automobile engine supports, bridge supports, shock absorbers, pads and various shock-absorbing blocks. The product has shock absorption, wear resistance, 2YLYY18 has excellent aging resistance and can maintain good performance after long-term use. In actual production, EPDM reclaimed rubber can be used alone or in combination with EPDM rubber. The usage and dosage can be determined according to the performance requirements of the shock-absorbing material and the specific indicators of the reclaimed rubber.
2. Formula design of EPDM reclaimed rubber shock absorption material
(1) Vulcanization system: When using EPDM reclaimed rubber to produce shock-absorbing materials, ordinary sulfur vulcanization system is generally used, especially for shock-absorbing products with larger sizes. Properly increasing the amount of sulfur can increase the cross-linking density of the rubber compound, increase the stiffness of the vulcanizate, reduce the damping coefficient and dynamic ratio, reduce heat generation, slow down creep and stress relaxation, and improve mechanical and dynamic properties. It should be noted that too much cross-linking density will cause the strength of the vulcanizate to decrease and fatigue damage shortened, so the amount of sulfur should be appropriately controlled.
When choosing an accelerator with sulfur in the EPDM reclaimed rubber shock absorption material, an accelerator that can appropriately extend the scorch time and increase the vulcanization rate should be selected.
(2) Reinforcement system: Choosing a suitable reinforcement system can significantly improve the mechanical strength and wear resistance of the EPDM reclaimed rubber vulcanizate. When using EPDM reclaimed rubber to produce shock-absorbing materials, it is generally used in combination with fast-pressed black and semi-reinforced carbon black with medium reinforcement performance. Commonly used are N550 and N774, which have good dynamic performance; when the damping performance is relatively high , Can be used with high wear-resistant carbon black such as N330.
Silica has the effect of delaying vulcanization and is not recommended. As the filler, mica powder, graphite powder, etc. having a lamellar structure can be used.
(3) Softening system: Choosing a suitable softener can improve the process performance of the EPDM compound and reduce the cost, but too much softener will cause the dynamic performance of the compound to deteriorate, creep and stress relaxation increase, thereby shortening the reduction. To reduce the life of shock products, the amount of softener should be appropriately reduced.
In actual production, when using EPDM reclaimed rubber to prepare shock-absorbing materials, factors such as the use of the anti-aging system and the setting of rubber processing conditions will also affect the shock-absorbing effect of the rubber. The editor will have the opportunity to continue discussing with you later.
Exclusive original article [commercial authorization] reprint, excerpt and excerpt in any form are prohibited without written authorization. Focus on Hongyun rubber: learn the process formula and raw material technology of producing rubber products from recycled rubber to help you reduce costs and increase profits