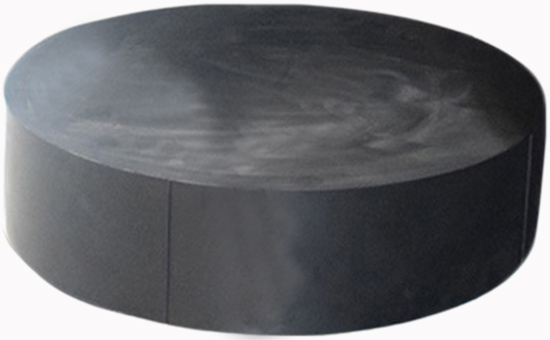
Rubber bearings are mainly used to support the weight of containers or equipment, as well as vibration or seismic loads generated during operation. Natural rubber is the main raw material for the production of various rubber bearings. For example, sheet rubber bearings are generally composed of multiple layers of natural rubber and some steel plates. In actual production, natural rubber can be combined with different types and dosages of compounding agents to produce rubber bearings with a variety of indicators and specifications to meet the needs of different use occasions.
1. Reference formula for rubber bearing produced by pure natural rubber
(1) 100 parts of natural rubber, 6 parts of zinc oxide, 1 part of stearic acid, 5 parts of antioxidants, 15 parts of carbon black, 2 parts of engine oil, 0.7 parts of accelerator, 2.5 parts of sulfur; total: 132.2 parts. Vulcanized rubber hardness (Sauer A type): 50 degrees.
(2) 100 parts of natural rubber, 10 parts of zinc oxide, 1 part of stearic acid, 5 parts of antioxidants, 35 parts of carbon black, 2 parts of engine oil, 0.7 parts of accelerator, 2.5 parts of sulfur; total: 156.2 parts. Vulcanizate hardness (Sauer A type): 60 degrees.
(3) 100 parts of natural rubber, 30 parts of zinc oxide, 1 part of stearic acid, 5 parts of antioxidant, 60 parts of carbon black, 2 parts of engine oil, 0.7 parts of accelerator, 2.5 parts of sulfur; total: 201.2 parts. Vulcanized rubber hardness (Sauer A type): 70 degrees.
2. Formulation process of rubber bearing produced by pure natural rubber
When using natural rubber alone to produce rubber bearings with different hardnesses, the physical properties of the product can be adjusted by adjusting the types and amounts of rubber additives. In actual production, carbon black is a commonly used reinforcing agent for natural rubber products. The combination of high wear-resistant carbon black and semi-reinforcing carbon black can further coordinate the tensile strength, elongation at break, tensile stress, and hardness of the rubber support. , Tearing performance, wear resistance and other relations. For example, non-polluting high-constant elongation semi-reinforcing furnace black N774 vulcanizate has good process performance, high elasticity of the product, low heat generation, and good dynamic performance.
3. The advantages and disadvantages of pure natural rubber production of rubber bearings
The rubber bearing made entirely of natural rubber has high strength, wear resistance, tear resistance, good low temperature resistance, and can be used in the area of minus 40 ℃. However, natural rubber itself has poor aging resistance such as ozone resistance and weather resistance. The rubber bearing 2YLYY1119 needs to work in harsh environments for a long time; therefore, rubber bearing manufacturers often use natural rubber as the main raw material in the rubber bearing formulation Appropriate addition of styrene butadiene rubber, butadiene rubber, neoprene, etc., to further improve the aging resistance of natural rubber bearings.
In terms of production costs, natural rubber prices are quite high and the price fluctuates greatly. In order to reduce costs and better control costs, rubber bearing manufacturers can also use synthetic rubber with a lower price than natural rubber in the formulation, or add appropriate amounts Reclaimed rubber can effectively reduce the cost of raw materials under the premise of ensuring the quality of the finished product. Later editors will continue to discuss related issues with you.
Exclusive original article [commercial authorization] reprint, excerpt and excerpt in any form are prohibited without written authorization. Focus on Hongyun rubber: learn the process formula and raw material technology of producing rubber products from recycled rubber to help you reduce costs and increase profits