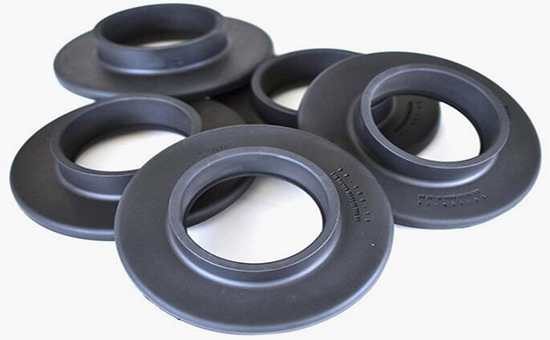
The use of nitrile reclaimed rubber instead of nitrile rubber to produce oil-resistant rubber products, wear-resistant parts, and shock-absorbing products can significantly reduce the cost of raw materials, and on this basis, shorten the rubber compound mixing cycle and improve the quality of the nitrile reclaimed rubber compound. Production costs can be further saved. So what methods should the nitrile reclaimed rubber products manufacturer choose to shorten the mixing time and reduce the production cost?
1. Select the rubber compound
The nitrile reclaimed rubber is a reclaimed rubber processed from nitrile hydroxyl rubber or waste nitrile rubber. The molecular weight of the nitrile reclaimed rubber processed by different raw materials is different. Generally, the higher the average molecular weight, the narrower the molecular weight distribution. The shorter the mixing time of the nitrile reclaimed rubber in the internal mixer; the powdered nitrile rubber is easier to mix than the bulk nitrile rubber, so the addition of an appropriate amount of powdered nitrile rubber in the production of nitrile reclaimed rubber products can also be reduced. Recycled rubber mixing time.
2. Reasonable design and cooperation system
The rubber filler is the most used component of the nitrile reclaimed rubber product except the rubber. Carbon black is the most commonly used product. The soft black carbon black will produce a lot of fine powder, which takes longer to infiltrate, so the most It is good to avoid the use of carbon black with particularly soft particles; the carbon black with low specific surface area has better dispersibility in the nitrile reclaimed rubber, and the carbon black with high structure can improve the viscosity of the rubber, increase the shearing force and promote the dispersion; Ensure that the carbon black is quickly dispersed evenly in the nitrile reclaimed rubber. It is better to use carbon black with large particle size and high structure to meet the other performance requirements, so as to improve the mixing efficiency of the reclaimed rubber.
The processing of nitrile reclaimed rubber is inseparable from the combination of other inorganic fillers and rubber oil. The aromatic hydrocarbon oil can shorten the mixing time of the nitrile reclaimed rubber; the mixing time of the talcum powder in the rubber compound is shorter than other white fillers. Used in the production of light-colored nitrile reclaimed rubber products, shortening the mixing time; while in the processing of nitrile reclaimed rubber foaming products, the organic foaming agent has better dispersibility than the inorganic foaming agent in the rubber compound. Nitrile reclaimed rubber products manufacturers can choose organic foaming agent to properly shorten the mixing time of nitrile reclaimed rubber.
3. Treatment of compounding agents
Sulfur is the most commonly used vulcanizing agent in the processing of nitrile reclaimed rubber products, but traditional sulfur is difficult to disperse rapidly and uniformly in nitrile reclaimed rubber; magnesium carbonate is white monoclinic crystal or amorphous powdery material, in the processing of rubber products It can be used as a reinforcing agent and a filler. In the production of nitrile reclaimed rubber products, the treatment of sulfur with magnesium carbonate can significantly increase the dispersion speed of sulfur in the nitrile reclaimed rubber, thereby reducing the mixing time.
When a foamed rubber product is produced using a nitrile reclaimed rubber, a foaming agent is indispensable, but a blowing agent such as sodium hydrogencarbonate is difficult to uniformly disperse in a nitrile reclaimed rubber, and oil or The wax coats the sodium bicarbonate to improve the dispersion of the foaming agent in the rubber compound and shorten the mixing time of the nitrile reclaimed rubber.
4. Using processing aids
The relative molecular weight of the resin is relatively high. It is solid, medium solid and liquid at normal temperature. It has a softening or melting temperature range. It has a tendency to flow under the action of external force. It can be used as a homogenizer in the nitrile reclaimed rubber product to promote uniform dispersion of the compounding agent and reduce Mixing time.
5. Control the amount of mixing and the speed of the mixer
In order to ensure the mixing uniformity and mixing effect, the mixing process of the nitrile reclaimed rubber products is mostly carried out in an internal mixer. It is possible to shorten the mixing time by experimentally knowing the optimum mixing amount of the internal mixer used. The optimum mixing amount of nitrile reclaimed rubber with different rubber content in the internal mixer is different; increasing the rotor speed of the internal mixer is also an effective method to reduce the mixing time, but in actual operation, the internal speed of the internal mixer is fast. The heat is also fast and requires an efficient cooling system.
Everything has positive and negative aspects. For example, the method of shortening the vulcanization time by adjusting the vulcanization temperature and improving the production efficiency of the regenerated rubber product of nitrile has its own defects. Unrestricted increase of the vulcanization temperature of the nitrile reclaimed rubber will result in The quality of nitrile vulcanizate is obviously reduced. Also, there are some shortcomings in shortening the mixing time of nitrile reclaimed rubber by suitable methods. Rubber product manufacturers must look at the problem from a global perspective when selecting one or several methods. Don't lose quality for cost.
Exclusive original article [commercial authorization] reprint, excerpt and excerpt in any form are prohibited without written authorization. Focus on Hongyun rubber: learn the process formula and raw material technology of producing rubber products from recycled rubber to help you reduce costs and increase profits