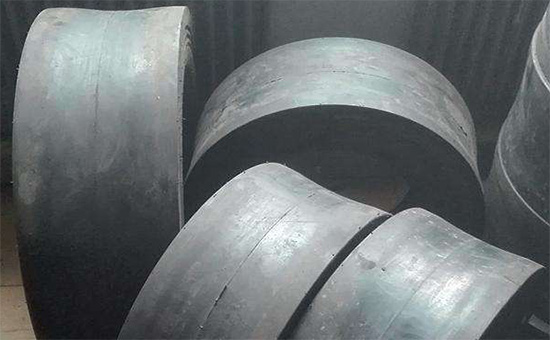
The roller compact tire is used for compaction of asphalt pavement and requires long-term contact with asphalt and other oil substances. Smooth tires made of natural rubber, styrene-butadiene rubber, and butadiene rubber are poor in oil resistance and prone to swelling. The problem is that nitrile reclaimed rubber with excellent oil resistance can improve the oil resistance of smooth tires and avoid swelling and sticky stone problems in asphalt. Then, how to use nitrile reclaimed rubber in smooth tires? What should be paid attention to in the production process?
A three-stage mixing process with a glossy tire rubber blended with nitrile reclaimed rubber. 1Mixing process feeding sequence: natural rubber, styrene-butadiene rubber, nitrile reclaimed rubber, zinc oxide, stearic acid, etc. → pressure and pressure 砣 → 1/2 carbon black and aromatic oil → pressure and pressure 砣 → pressure 砣 → row Adhesive; 2 two-stage mixing process feeding sequence: a period of mixing rubber → pressure pressure 砣 → pressure 砣 → 1/2 carbon black → pressure 砣 → pressure 砣 → rubber row; 3 three-stage mixing process feeding sequence: Two-stage mixing compound → sulfur and accelerator → pressure and pressure → pressure lifting → pressure and pressure → pressure lifting → pressure and pressure → pressure lifting → debinding. The rubber compound is generally vulcanized in a vulcanizing press. The vulcanization conditions are 143°C x 45 minutes. The vulcanization performance of the glossy tire rubber compounded with nitrile rubber reclaimed rubber and the vulcanization performance of the rubber material without the nitrile rubber reclaimed rubber were similar, and the vulcanization speed basically had no effect.
From a performance point of view, the finished tires with nitrile rubber reclaimed rubber can meet the relevant national standards in terms of tensile strength, wear resistance, and adhesiveness. The oil resistance is greatly improved, and the smooth surface tires are laid in asphalt pavements. Swelling problem prolongs the service life of glossy tires. From the perspective of cost, the price of nitrile reclaimed rubber is significantly lower than that of natural rubber and styrene-butadiene rubber. Substituting some raw rubber for the production of glossy tires can significantly reduce raw material costs.
When choosing nitrile reclaimed rubber blended with glossy tires, it is best to use a high nitrile-containing reclaimed rubber with a rubber hydrocarbon content of more than 30% to ensure that the glossy tire has good resistance to liquids and oils.
Attachment: Natural rubber, 40 parts; SBR, 60 parts; Nitrile reclaimed rubber, 30 parts; Carbon black, 58 parts; Sulfur, 2.1 parts; Active agent, 7 parts; Antioxidant, 4 parts; Aromatic oil, 10 Parts; other ingredients, 5 parts; anti-coke agent, 0.1 parts.
Exclusive original article [commercial authorization] reprint, excerpt and excerpt in any form are prohibited without written authorization. Focus on Hongyun rubber: learn the process formula and raw material technology of producing rubber products from recycled rubber to help you reduce costs and increase profits