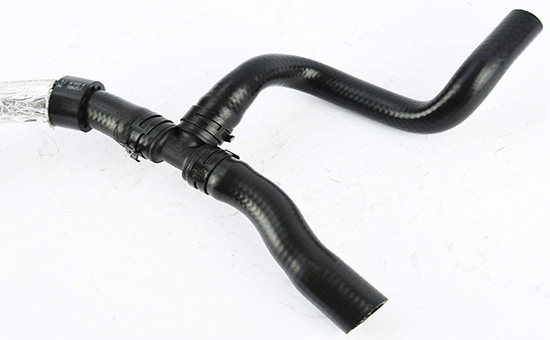
EPDM rubber has excellent high temperature resistance and can be used to produce radiator hoses. Adding proper amount of EPDM reclaimed rubber to EPDM radiator hose can reduce raw material cost and production cost; however, in the application process, Many EPDM radiator hoses have material deposits on the inner wall of the EPDM radiator, which causes blockage of the heat-dissipating pipes. Manufacturers who use EPDM reclaimed rubber to produce radiator hoses believe that the reclaimed rubber itself contains impurities, but is this really the case?
1. The cause of material deposition in the heat-dissipating hose
Regardless of whether the EPDM hose contains EPDM reclaimed rubber or does not contain EPDM reclaimed rubber, it may cause material deposition on the inner wall surface. This is because the sulfur vulcanization system is usually used when vulcanizing EPDM rubber. Zinc oxide, stearic acid or zinc salt promoter, soluble zinc salt is the main factor causing the deposition of the inner wall of the hose; the low solubility accelerator in the vulcanization system will also promote the deposition of the inner wall of the hose; many EPDM cooling hoses are filled A large amount of mineral fillers also promote the formation of sedimentary materials.
2. Ways to reduce material deposition on the inner wall of the heat-dissipating hose
Whether the EPDM heat-dissipating hose produces material deposition is directly related to the coolant's extraction of the rubber compound. Tests have shown that the content of the EPDM/recycled vulcanizate using peroxide vulcanization is only 10% of the sulfur vulcanizate. At this time, the content of the extract in the coolant is greatly reduced, and the surface of the inner wall of the hose is deposited. The chances of hindering the normal operation of the cooling system are naturally greatly reduced.
Therefore, when using EPDM rubber or EPDM rubber to produce radiator hose, peroxide vulcanization can be selected. When sulfur vulcanization is used, it is best to use an effective vulcanization system with low sulfur content to reduce the deposition of material on the inner wall of the hose. At the same time, it can also improve the heat resistance and compression set resistance of the rubber compound; however, in the actual operation process, the peroxide is easily affected by oxygen when it is steam vulcanized EPDM rubber, resulting in hot tearing performance of the rubber compound. Deterioration, so special care is required during vulcanization molding.
Xiaobian can't say that the radiator hose produced by using EPDM reclaimed rubber has no relationship with the EPDM reclaimed rubber during the use. After all, if the quality of the reclaimed rubber you use is problematic, then everything is said. White; but when choosing high-quality EPDM reclaimed rubber to replace some EPDM rubber to produce radiator hose, there is really little relationship between material deposition and reclaimed rubber on the inner wall of the hose; therefore, when using recycled rubber to reduce costs, it must be Regular manufacturers choose reclaimed rubber with relevant testing standards.
Exclusive original article [commercial authorization] reprint, excerpt and excerpt in any form are prohibited without written authorization. Focus on Hongyun rubber: learn the process formula and raw material technology of producing rubber products from recycled rubber to help you reduce costs and increase profits