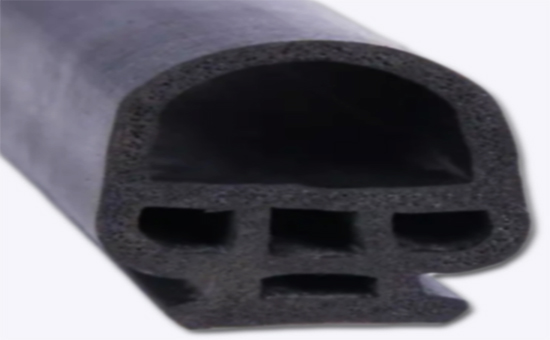
EPDM rubber has excellent ozone resistance, weather resistance, heat resistance, etc., and is widely used in the automotive industry, construction industry, electrical and electronic fields. However, in actual production, EPDM rubber has some "congenital defects" due to the characteristics of its molecular structure, which are mainly manifested in poor self-adhesion and mutual adhesion, high raw rubber price, slow vulcanization speed, oil resistance, flame retardant and resistance. Poor air tightness and other shortcomings; then how should manufacturers of EPDM rubber products overcome these shortcomings?
1. How to solve the problem of poor adhesion of EPDM rubber
There is a lack of active groups in the molecular structure of EPDM rubber, low cohesive energy, poor self-adhesion and mutual adhesion; it is easy to cause delamination problems. In actual production, the combination of EPDM rubber and rubber with good adhesion can improve the adhesion of EPDM vulcanizates, such as combined use with natural rubber with good self-adhesion; NR/EPDM blend rubber chooses sulfur-peroxide The vulcanization system further improves the self-adhesion of the rubber compound. To improve the adhesion of EPDM rubber, tackifying resins can also be used to avoid or reduce the amount of additives that are easy to cause blooming, such as degradants, oils, paraffins, sulfur, waxes, etc.
From the production process point of view, to improve the self-adhesion and mutual viscosity of EPDM rubber, the mixing temperature can be appropriately lowered, or two-stage mixing can be used; the mixing time can be appropriately increased so that the mixed rubber compound 2ELYY412 has a lower Mooney viscosity. The calendered film needs to be rapidly cooled, and the cooling rate of the calendered film or extruded rubber compound needs to be carefully controlled to improve self-adhesion.
2. How to solve the problem of high price of EPDM rubber
At present, EPDM is widely used in the field of non-tire rubber products, but the price of raw rubber is relatively high among synthetic rubber products, higher than that of styrene-butadiene rubber, butadiene rubber, isoprene rubber, nitrile rubber, etc. For EPDM rubber product manufacturers, the cost input is relatively large. In this regard, I have two suggestions:
(1) Increase the amount of filler and rubber oil. EPDM rubber is a low-density rubber, and a large amount of fillers and rubber oil can be added; especially for Gao Mooney's EPDM rubber, the physical and mechanical properties of the rubber compound after high filling are not greatly reduced; Production costs, alleviate the problem of high price of EPDM raw rubber, and better control costs.
(2) Appropriate use of waste rubber resources: In actual production, EPDM unvulcanized rubber compound, leftovers of EPDM rubber products, and waste EPDM rubber products can be sorted, desulfurized, refined, molded, etc. The process is processed into EPDM reclaimed rubber, which retains the basic performance characteristics of EPDM raw rubber, and the price is much lower than that of raw rubber. It can replace a certain proportion of EPDM rubber production products according to actual needs, effectively reducing the cost of raw materials. In the production of EPDM rubber products, if necessary, a small amount of waste rubber regeneration resources such as butyl reclaimed rubber and vulcanized rubber powder can be added to improve the comprehensive performance of rubber products and reduce production costs.
Exclusive original article [commercial authorization] reprint, excerpt and excerpt in any form are prohibited without written authorization. Focus on Hongyun rubber: learn the process formula and raw material technology of producing rubber products from recycled rubber to help you reduce costs and increase profits