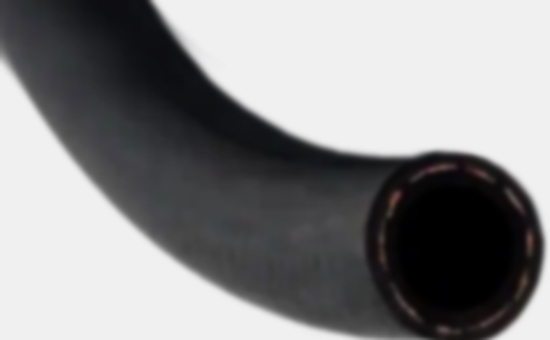
Nitrile rubber has excellent oil resistance, good heat resistance, wear resistance and aging resistance, and is an ideal raw material for the production of oil-resistant hoses and hydraulic hoses, especially inner hoses. When using nitrile rubber as the main raw material to produce oil-resistant hoses, an appropriate amount of neoprene is added to improve the ozone resistance and aging resistance of oil-resistant cloth hoses; The appropriate use of reclaimed rubber can further improve the processing performance of rubber while reducing costs.
1. Nitrile rubber/neoprene/reclaimed rubber is used to produce oil-resistant cloth cloth hose inner rubber vulcanization formula
(1) 50 parts of nitrile rubber, 50 parts of neoprene, 10 parts of reclaimed rubber, 5 parts of zinc oxide, 2.5 parts of stearic acid, 4 parts of magnesium oxide, 0.5 parts of antioxidant A, 1 part of antioxidant D, 1 part of paraffin, 50 parts of carbon black N660, 25 parts of light calcium, 30 parts of clay, 6 parts of pine tar, 13 parts of dibutyl phthalate, 10 parts of coumarone resin, 0.5 parts of accelerator DM, 0.3 parts of accelerator TMTD; Total: 258.8 shares.
(2) 60 parts of nitrile rubber, 40 parts of neoprene, 20 parts of reclaimed rubber, 4 parts of zinc oxide, 1.5 parts of stearic acid, 3 parts of magnesium oxide, 1 part of antioxidant A, 1.5 parts of antioxidant D, 1 part of paraffin, 40 parts of carbon black N330, 70 parts of light calcium, 12 parts of dibutyl phthalate, 6 parts of third-line oil, 8 parts of coumaron resin, 8 parts of asphalt, 2.4 parts of accelerator DM; Total: 278.4 copies.
(3) 70 parts of nitrile rubber, 30 parts of neoprene, 50 parts of reclaimed rubber, 5 parts of zinc oxide, 2 parts of magnesium oxide, 1.5 parts of stearic acid, 1.5 parts of antioxidant A, 1 part of antioxidant D, 30 parts of carbon black N330, 10 parts of carbon black N660, 33 parts of light calcium, 25 parts of clay, 8 parts of dibutyl phthalate, 5 parts of engine oil, 6 parts of asphalt, 10 parts of coumaron resin, 1.8 parts of accelerator DM, 0.3 parts of accelerator CZ, 0.5 parts of sulfur, 1 part of phthalic anhydride; Total: 291.6 parts.
2. Nitrile rubber/neoprene/reclaimed rubber is used to produce oil-resistant cloth hose inner rubber formula design
In the formulation design of the inner layer of the oil-resistant cloth hose, nitrile rubber, as the main material, provides excellent oil resistance and mechanical properties, and the addition of neoprene further enhances the ozone resistance and aging resistance E4LYY521 of the rubber compound. The use of reclaimed rubber can effectively reduce the production cost on the premise of ensuring the performance of the inner layer of the oil-resistant hose. When designing the inner rubber formula of oil-resistant cloth clamping hose containing reclaimed rubber, it is necessary to comprehensively consider a variety of factors, including the selection of rubber type, the construction of vulcanization system, the matching of filler system and the use of softening plasticizers, so as to improve the processing performance of rubber compounds, improve the quality of finished products, and reduce costs.
(1) Vulcanization system
The vulcanization system has a decisive influence on the performance of oil-resistant cloth hoses. When nitrile rubber/neoprene/reclaimed rubber is used to produce the inner layer of the cloth rubber compound, the selection of the vulcanization system should be determined according to the content of neoprene. When the content of neoprene is high, a vulcanization system suitable for neoprene should be used to ensure the uniformity of the vulcanization process and the performance of the hose.
(2) Filling system
The packing system has an important influence on the mechanical properties and processability of the oil-resistant cloth hose. In actual production, the inner layer of oil-resistant cloth cloth hose reinforcing filling system mixed with reclaimed rubber combines high wear-resistant carbon black (such as N330) or general carbon black (such as N660) with semi-reinforcing carbon black (such as N774), which can provide good reinforcing effect and processing performance. Appropriate amount of light calcium and clay is filled to further improve the flexibility and processing performance of the rubber compound.
(3) Softening system
The selection of softening plasticizer should take into account the oil resistance and processability of the oil-resistant hose. In the combined compound of nitrile rubber/neoprene/reclaimed rubber, ester softening plasticizers can usually provide better plasticizing effects. It should be noted that the use of softening plasticizers should be minimized to avoid affecting the oil resistance and mechanical properties of the hose.
The appropriate amount of reclaimed rubber is used in the inner layer of the oil-resistant cloth hose, and the rubber compound formula is reasonably designed, which can not only ensure the good oil resistance, aging resistance and mechanical properties of the inner layer of the oil-resistant hose, but also effectively reduce the production cost and improve the production efficiency. With the continuous progress of reclaimed rubber production technology, the application of reclaimed rubber in oil-resistant cloth hoses will become more and more extensive.
Exclusive original article [commercial authorization] reprint, excerpt and excerpt in any form are prohibited without written authorization. Focus on Hongyun rubber: learn the process formula and raw material technology of producing rubber products from recycled rubber to help you reduce costs and increase profits