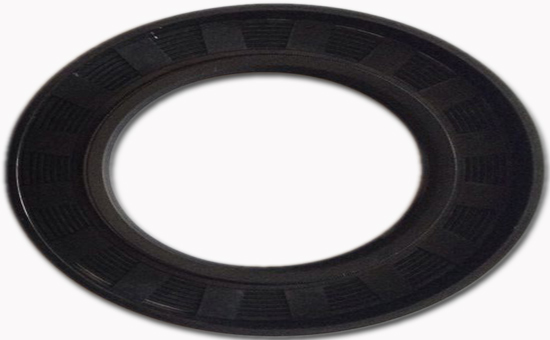
The vulcanization process is a process in which the rubber is combined with vulcanizing agents, accelerators and other cross-linking aids to transform linear macromolecules into a three-dimensional network structure at a specific temperature and pressure. It is the last major process in the processing of rubber products. The vulcanization effect directly affects the performance of the finished product. When using nitrile rubber to produce rubber products, strictly follow the production process formula and production procedures to effectively improve the yield of nitrile rubber products.
1. Adhesion of overflow glue
When the nitrile rubber is vulcanized, to prevent the adhesion of the overflow glue, an appropriate amount of silicone coupling agent or high-structure carbon black can be used to increase the crosslinking density of the nitrile vulcanizate. Properly adjust the vulcanization temperature and formula vulcanization system to make the vulcanization curve of butyronitrile 2YLYY813 fully flat; add an appropriate amount of softener that is easy to bloom during vulcanization and molding. From the perspective of process operation, take out the molded product within the most appropriate vulcanization time; better vulcanization temperature is about 150℃, avoid vulcanization at a temperature higher than 170℃, and effectively prevent the adhesion of overflow glue.
2. The rubber blank is cut off
When the rubber blank is cut off during the vulcanization of the nitrile rubber, the tear strength needs to be appropriately reduced, the rubber material maintains good fluidity, and the overflow rubber is reduced. From the formulation point of view, it is recommended to choose rubber with good fluidity (such as adding a small amount of nitrile reclaimed rubber), reduce the rubber content, increase the crosslinking density of the rubber compound, or use a low-viscosity compounding agent to appropriately extend the scorch time by adjusting the vulcanization system. From the point of view of operating procedures, appropriately lowering the vulcanization temperature and reducing the amount of feed can also effectively prevent the rubber blank from breaking during nitrile vulcanization.
3. Releasability
The basic idea to improve the mold release of nitrile rubber is to prevent mold sticking. From the formulation process, use a proper amount of mold release agent, pay attention to mold contamination and blooming; increase the cross-linking density of the rubber compound and increase the high temperature tear strength; use a system that will not pollute the mold; if the formula contains magnesium oxide, it is required Reduce the performance of magnesium oxide and improve the release properties of nitrile rubber. From the point of view of the operation process, applying a proper amount of release agent on the mold can also significantly improve the release performance of the nitrile vulcanizate.
Nitrile rubber can be used to produce various oil-resistant rubber products, rubber gaskets, rubber tubes, printing and dyeing rubber rollers, cable rubber materials, etc. It is widely used in the fields of automobiles, aviation, petroleum, and copying. Vulcanization is an important process in the production process of nitrile rubber products. Avoiding failures during vulcanization can effectively improve the performance and yield of nitrile rubber products. The next edition will continue to share with you other common problems and solutions during nitrile rubber vulcanization. .
Exclusive original article [commercial authorization] reprint, excerpt and excerpt in any form are prohibited without written authorization. Focus on Hongyun rubber: learn the process formula and raw material technology of producing rubber products from recycled rubber to help you reduce costs and increase profits