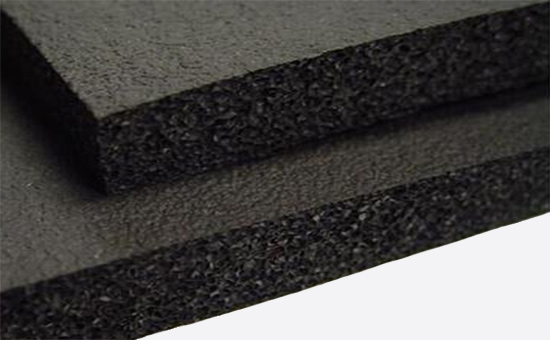
Sponge foam rubber products processed with natural rubber as the main raw material have hot spots such as low density and good elasticity, and have significant sound absorption and shock absorption effects. They are widely used in applications such as sealing, shock absorption, and noise reduction. In actual production, the shrinkage of natural rubber sponge products affects the performance and life of the finished product. Rubber product manufacturers need to take certain measures to improve the shrinkage of natural rubber sponge products.
1. The significance of improving the shrinkage of natural rubber sponge products
When natural rubber sponge rubber is vulcanized at a certain temperature, the gas decomposed into foaming agent will generate a certain pressure to make the rubber sponge-like; the sponge rubber will be in a relatively stable state under the support of gas pressure. But with the continuous dissolution, penetration and diffusion of gas in the natural rubber, the internal gas pressure 2LLYY1022 will decrease; after the pressure is reduced, the natural rubber sponge rubber will shrink to a certain extent during the foaming process, resulting in sponge products The stability becomes poor during storage and use.
2. Ways to reduce the shrinkage of natural rubber sponge products
When using natural rubber to prepare sponge rubber, factors such as the type of rubber and the amount of rubber in the formula will affect the shrinkage of foam rubber. Rubber products manufacturers can start from the following aspects to reduce the shrinkage of natural rubber sponge products.
(1) Control the glue content
In actual production, natural rubber sponge foam products have relatively large rubber content, which is beneficial for rubber foaming, but the larger the rubber content, the greater the possibility of shrinkage of the sponge rubber, so appropriately reduce the rubber content. The amount can reduce the shrinkage of the rubber. It should be noted that when the rubber content of the natural rubber sponge foam rubber material is less than 30%, the foam rubber material is difficult to foam, so the rubber content should not be too low, and the rubber content of natural rubber sponge products needs to be controlled reasonably.
(2) Use butadiene rubber with caution
Natural rubber sponge products are often used together with butadiene rubber in the production process. The permeability of gas in different rubbers is different, and the permeability in butadiene rubber is the largest; therefore, when NR/BR is used in combination, the greater the amount of butadiene added, the greater the shrinkage of the sponge rubber. When mixing butadiene rubber in natural rubber sponge products, the dosage must be controlled reasonably. If necessary, an appropriate amount of styrene butadiene rubber can be added to reduce the shrinkage of the natural rubber/butadiene rubber sponge rubber.
When natural rubber/butadiene rubber is used in combination, with the increase in the amount of butadiene, the greater the probability that the combined rubber compound will be mixed and released, the appropriate use of styrene butadiene rubber can improve the process performance of the combined rubber compound to a certain extent.
(3) Combined use of rubber and plastic
Plastic has a small permeability to gas and forms a rigid skeleton after being plasticized and cooled by heat during the vulcanization process. When using natural rubber to produce sponge foam rubber products, rubber product manufacturers can use plastic in the formula to effectively prevent shrinkage and reduce the shrinkage of natural rubber sponge rubber. In theory, adding about 20 parts of plastic to the formula of natural rubber sponge products can effectively avoid shrinkage of the rubber. It should be noted that the addition of plastic will cause the permanent deformation of the sponge rubber to increase, and the dosage needs to be controlled reasonably.
(4) Use resin
Thermoplastic resins such as phenolic resin and polymerized rosin resin can improve the rheological properties of the rubber material, which is not only beneficial to the foaming process, but also has a certain reinforcing effect. It improves the rigidity of natural rubber sponge products while reducing the shrinkage of the sponge rubber. In actual production, phenolic resin has a high melting point and is difficult to disperse in natural rubber. It is recommended to heat phenolic resin before use.
(5) Use reclaimed rubber
Experiments show that mixing natural rubber with an appropriate amount of reclaimed rubber can reduce the swelling or shrinkage of the rubber material during processing, improve the rubber processing technology and the accuracy of the finished product size and shape, and improve the shrinkage of natural rubber sponge products.
Exclusive original article [commercial authorization] reprint, excerpt and excerpt in any form are prohibited without written authorization. Focus on Hongyun rubber: learn the process formula and raw material technology of producing rubber products from recycled rubber to help you reduce costs and increase profits