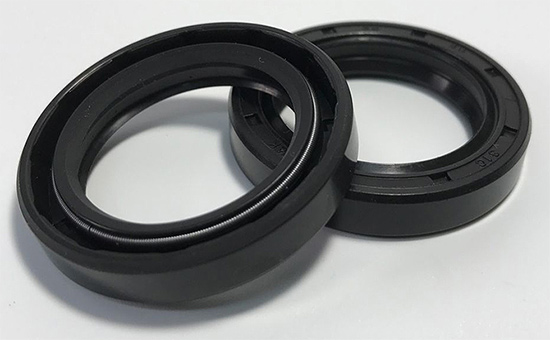
Generally, the oil seals working in the environment below 120 °C will be made of nitrile rubber. Now many rubber products manufacturers will use a certain proportion of nitrile reclaimed rubber in nitrile oil seal to reduce the cost of raw materials. In actual use, the hardness of nitrile seal is different for different applications. There are certain differences. When rubber rubber seals are produced using nitrile rubber and nitrile reclaimed rubber, the rubber compound, vulcanization system and reinforcing system in each oil seal formula are different.
1. Different hardness of nitrile oil seals used in different rubber compounds
There are various kinds of nitrile rubber and nitrile reclaimed rubber on the market. Different origins and different grades of nitrile rubber have different hardness. Generally, they are divided into three types: Shore 70, 80, and 90 degrees. The nitrile oil seal used in the case of large voids selects high-hardness nitrile rubber to prevent oil seal damage and prolong the use time. (Because the hardness of nitrile rubber is too high, it will bring certain difficulties to processing and use, so it is necessary to integrate Considering its hardness), nitrile rubber 2707 and 3704 are ideal materials for producing high hardness nitrile oil seals; nitrile reclaimed rubber is used as a rubber for recycling and reprocessing of waste nitrile products, and the hardness is also very different. Oil seal hardness requirements Select a suitable hardness of the nitrile reclaimed rubber to be used in the oil seal.
2. Different hardness of nitrile oil seal vulcanization system is different
When producing an oil seal using nitrile rubber/recycled rubber, a sulfur vulcanization system is often used, and two or more accelerators are used. Since the hardness of the nitrile rubber product increases with the increase of the amount of sulfur, the amount of sulfur in the high hardness nitrile oil seal should be increased as much as possible without meeting the frost and smoke; the accelerator CZ is a height. The active after-effect accelerator can be used together with the accelerator TMTD to produce oil seals with low hardness, good anti-scorch performance, high processing safety and good comprehensive performance.
In high-hardness oil seal products, rubber products manufacturers can use accelerator DM, accelerator TMTD, and accelerator D together. The nitrile oil seal has good vulcanization performance, large elongation at break, high tensile strength, and can be adjusted by adjustment. The dosage of the agent can be used to adjust the vulcanization rate; in addition, the rubber product manufacturer can also use sulfur and DPC to produce a high-hardness nitrile oil seal to further improve the compression set resistance, tensile stress, hardness, tensile strength and heat resistance of the oil seal.
3. Different hardness of nitrile oil seal reinforcement system is different
The most common way to adjust the hardness of rubber products in the rubber products industry is to adjust the type and amount of carbon black. Therefore, in the nitrile rubber/recycled rubber seal, the types and amounts of carbon black used for nitrile seals with different hardness are very different, generally low. The hardness of the nitrile oil seal can use semi-reinforcing carbon black, spray carbon black such as N550, N774, and the higher hardness oil seal uses semi-reinforcing carbon black, high wear-resistant carbon black such as N660, N330, by adjusting different types of charcoal Black is added to obtain a nitrile oil seal of different hardness.
When using nitrile rubber/recycled rubber to produce nitrile oil seals, the formulas of different hardness products need to pay attention to the amount of softener, rubber oil type, anti-aging system design, etc., Xiaobian will not elaborate here.
Exclusive original article [commercial authorization] reprint, excerpt and excerpt in any form are prohibited without written authorization. Focus on Hongyun rubber: learn the process formula and raw material technology of producing rubber products from recycled rubber to help you reduce costs and increase profits