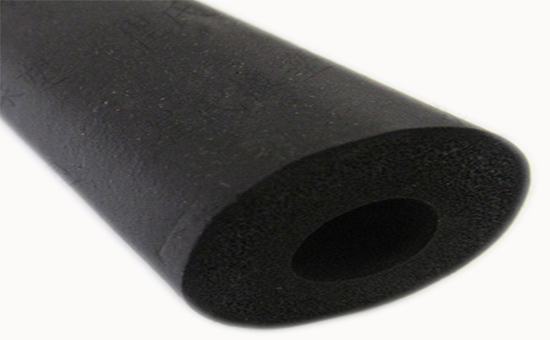
Sponge rubber has the characteristics of low density, good elasticity, flex resistance, etc., and has significant effects of shock absorption, sound insulation and heat insulation during use. EPDM rubber has excellent high and low temperature resistance, weather resistance, ozone resistance, etc. EPDM reclaimed rubber retains the basic performance characteristics of EPDM rubber, which can replace a certain proportion of EPDM rubber to produce sponge rubber sheets , Sponge rubber strips, sealing strips, insulation boards, sponge foam handles and other sponge products, which effectively reduce the cost of raw materials, among which the foaming system design is very important.
1. Commonly used foaming agent for EPDM sponge rubber
Rubber foaming agents are mainly divided into organic foaming agents and inorganic foaming agents. Thermally decomposed organic chemical foaming agents are mostly used when preparing various sponge rubber products using EPDM. The decomposition of the organic foaming agent 2YLYY823 is an exothermic reaction, and it decomposes rapidly after reaching a certain temperature, and the amount of gas is stable. The gas produced is mainly nitrogen, which has low permeability to rubber. Commonly used EPDM rubber/reclaimed rubber sponge foam products are foaming agent AC, foaming agent H, foaming agent OBSH, urea and so on.
2. The importance of matching the vulcanization speed of EPDM sponge rubber to the foaming speed
When using EPDM rubber or EPDM reclaimed rubber to produce various sponge foam rubber products, the vulcanization speed and foaming speed of the sponge rubber must match. In actual production, when the vulcanization speed of EPDM sponge rubber is faster than the foaming speed, the viscosity of the rubber increases, which is likely to cause difficulty in foaming; when the foaming speed of EPDM is faster than the vulcanization speed, the gas is easy to escape and the foaming rate Decrease, resulting in insufficient foaming, skinning, uneven surface and other problems, generally according to the vulcanization foaming curve to study the matching quality.
3. How to match the foaming speed and vulcanization speed of EPDM sponge rubber
In the formulation of EPDM sponge rubber, it is first necessary to select a foaming agent with a suitable decomposition temperature according to the molding process. At the same time, pay attention to the application of foaming aids, so that the decomposition of the foaming agent is carried out within the vulcanization controllable temperature range. In actual production, the decomposition rate of the foaming agent is greatly affected by the compounding agent in the rubber compound, and it is more difficult to adjust than the vulcanization rate. Therefore, after the foaming system is determined, the vulcanization system is usually adjusted to adapt to the foaming system.
When using EPDM rubber, EPDM reclaimed rubber or EPDM/reclaimed rubber combined to produce sponge foam rubber products, the rubber product manufacturer must select the appropriate variety of foaming agents and foaming aids, and adjust the vulcanization appropriately The system ensures that the foaming speed of EPDM sponge rubber matches the vulcanization speed, and the smooth foaming and molding of EPDM sponge rubber.
Exclusive original article [commercial authorization] reprint, excerpt and excerpt in any form are prohibited without written authorization. Focus on Hongyun rubber: learn the process formula and raw material technology of producing rubber products from recycled rubber to help you reduce costs and increase profits