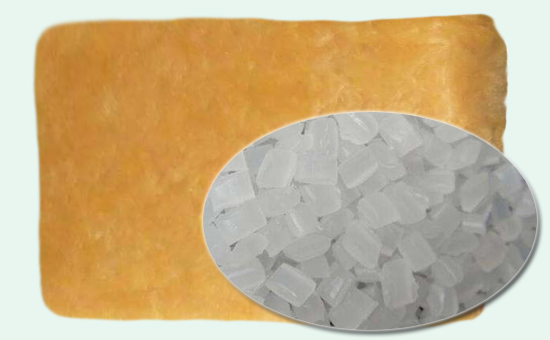
Natural rubber has high mechanical strength and good elasticity but can not be used to produce rubber products with special requirements for heat resistance, ozone resistance, oil resistance and gas permeability. It is often used together with other materials. Polymer is one of them; different types of polymerization The process performance and performance are different. Therefore, when adding a polymer to a natural rubber, it is necessary to adjust the mixing process in time according to the characteristics of the polymer itself; in actual production, natural rubber is often used together with polyethylene resin and EVA.
1. Combination of natural rubber and polyethylene resin
(1) Advantages of using natural rubber and PE together
Polyethylene resin is a kind of thermoplastic resin obtained by polymerization of ethylene. It is a PE that we often say has excellent low temperature resistance, good chemical stability and electrical insulation properties. It is insoluble in common solvents at normal temperature and can be used during use. It resists the erosion of most acids and alkalis; adding proper amount of polyethylene resin to natural rubber products can improve the chemical stability of natural rubber products.
(2) Natural rubber / polyethylene resin mixing skills
The natural rubber/PE blending material mixing process is generally carried out under the condition of 95-105 ° C, and the roll distance is between 1-2 mm. In the open mill, the polyethylene is first plasticized into a micro-transparent shape to make the roll. Then increase the roll distance to 4-5mm, add the same amount of natural rubber, then add the remaining natural rubber, adjust the roll distance to 1-2mm and then play the triangle for 10 times, the roll distance is increased to 4-5mm, the lower piece cool down. When the natural rubber/PE blend material is used in an internal mixer, a batch feeding method is generally employed.
2. Natural rubber and EVA combined
(1) Advantages of combining natural rubber with EVA
EVA is solid at room temperature, heated to a certain extent and becomes a liquid with a certain viscosity, which can flow, has good buffer, earthquake resistance, moisture resistance, chemical corrosion resistance, etc.; research shows that the production of natural rubber products with appropriate amount of EVA The weather resistance of the product can be significantly improved.
(2) natural rubber / EVA mixing skills
When natural rubber and EVA are used together, the rubber product manufacturer needs to first fully masticize the natural rubber, and the roll temperature is plasticized in the temperature range of 105-110 ° C to produce EVA, and the film is rolled; the natural rubber plasticized rubber-coated roll, the roll temperature is still controlled. Between 105-110 ° C; add an appropriate amount of EVA sheet, fully rolled, and then cooled.
Natural rubber has its own unique advantages, but also has its own defects. The combination with high polymer can obviously improve the comprehensive performance of natural rubber products. In addition, natural rubber can also be used together with other kinds of synthetic rubber and recycled rubber. After, the post-production will continue with you.
Exclusive original article [commercial authorization] reprint, excerpt and excerpt in any form are prohibited without written authorization. Focus on Hongyun rubber: learn the process formula and raw material technology of producing rubber products from recycled rubber to help you reduce costs and increase profits