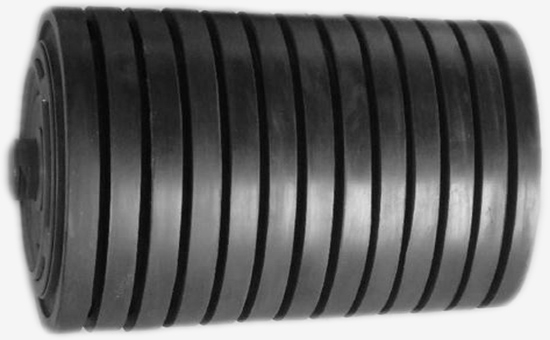
The rubber roller with natural rubber as the main raw material has the characteristics of high elasticity, small deformation, high wear resistance, and good process performance. It is widely used in the papermaking industry, printing and dyeing industry and various printers. However, with the continuous increase in the demand for rubber rollers in various industries and the increasingly fierce market competition, the use of natural rubber alone can no longer meet the needs of rubber rollers, and it needs to be used in conjunction with other polymers.
1. Synthetic rubber
Synthetic rubber is a synthetic elastomer, a highly elastic polymer synthesized by man-made, which can meet the different performance requirements of rubber products. Natural rubber has good compatibility with general synthetic rubber (styrene butadiene rubber, butadiene rubber, neoprene rubber, ethylene propylene rubber, butyl rubber, isoprene rubber, etc.). In actual production, the use of styrene butadiene rubber, butadiene rubber, neoprene rubber or butyl rubber in the rubber roller with natural rubber 2YLYY324 as the main raw material can significantly improve the aging resistance and chemical stability of the rubber roller.
Natural rubber can also be used with a small amount of polyurethane rubber to prepare rubber rollers with special properties.
2. Combined use of rubber and plastic
When using natural rubber to produce rubber rollers, natural rubber can be used together with high-pressure polyethylene resins, high-styrene resins, etc., to improve the process performance of the rubber roller and the performance of the finished product. Among them, high-pressure polyethylene resin is low-density polyethylene, which has the characteristics of low density, easy processing, good chemical stability, alkali resistance, organic solvent resistance, and electrical insulation. High styrene resin has the characteristics of good impact resistance. Adding natural rubber rubber rollers can significantly improve the flexural resistance and tear strength of the finished product.
3. Recycled rubber
Recycled rubber is the main raw material to reduce the cost of rubber products. In actual production, latex reclaimed rubber and tire reclaimed rubber have good compatibility with natural rubber and can directly replace natural rubber to produce various products, effectively reducing the cost of raw materials. When using natural rubber to produce rubber rollers, proper use of latex reclaimed rubber or tire reclaimed rubber can not only reduce the raw material cost and production energy consumption of the rubber roller, but also improve the anti-reactivity, shrinkage and compression set of the natural rubber vulcanizate.
When using natural rubber to produce rubber roller products, the use of synthetic rubber can improve the overall performance of rubber products, especially the aging resistance, and the use of low-priced synthetic rubber can also reduce the cost of raw materials. The combined use of rubber and plastic or the use of reclaimed rubber in natural rubber rubber rollers can not only reduce costs, but also improve the rubber processing technology and improve the aging resistance of rubber products. Later editors will continue to share the production formula of natural rubber rollers with you And production process.
Exclusive original article [commercial authorization] reprint, excerpt and excerpt in any form are prohibited without written authorization. Focus on Hongyun rubber: learn the process formula and raw material technology of producing rubber products from recycled rubber to help you reduce costs and increase profits