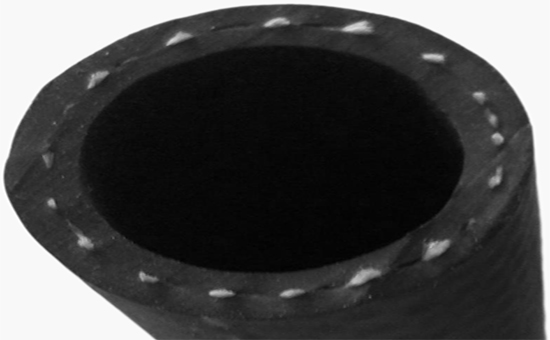
Nitrile rubber has excellent oil resistance, wear resistance, abrasion resistance, and strong adhesion. Nitrile reclaimed rubber retains the basic characteristics of nitrile rubber. Phenolic resin and nitrile rubber have good compatibility. When used as a reinforcing hardener and used in nitrile rubber, the combined vulcaniz Insulation is widely used in textile machinery, auto parts, electronic machinery, household products and other fields, such as washers, shoe soles, brake linings, acid-resistant gears, etc. A reasonable design formula can further improve the overall performance of the product.
1. Concurrent use ratio
Nitrile rubber, nitrile reclaimed rubber and phenolic resin can be miscible in any ratio. In the unvulcanized state, the phenolic resin has a plasticizing effect on the nitrile rubber; after vulcanization, the phenolic resin has a thermal curing effect on the rubber. To reinforcement. In actual production, nitrile rubber/reclaimed rubber generally uses two-stage thermosetting phenolic resin containing hexamethylenetetramine. When nitrile/phenolic resin is used together, the amount of phenolic resin is generally controlled below 75 parts, and the amount of nitrile rubber is recommended to be controlled at 45-50%.
In nitrile rubber/phenolic resin combined materials, when the amount of resin is increased to 100-250 parts, nitrile rubber acts as a plasticizer for phenolic resin and is generally used to prepare impact-resistant phenolic plastics.
2. Vulcanization system
When adding 50-100 parts of phenolic resin to nitrile rubber, nitrile reclaimed rubber or nitrile rubber/reclaimed rubber combined, sulfur vulcanization is generally used, with accelerator DM, etc., as the amount of phenolic resin 2YLYY1111 increases, the rubber hardness , Tear strength and tensile strength increase, but elongation at break and wear resistance decrease. In the formulation of high-hardness rubber products, when the amount of phenolic resin is greater than 100 parts, the rubber compound can be cross-linked without adding sulfur and accelerators.
3. Filling system
Inorganic fillers such as pottery clay and asbestos have a significant reinforcing effect in the combined rubber of nitrile rubber/phenolic resin; experiments show that when nitrile rubber/phenolic resin is used together in a ratio of 40/60, it can fill about 100-150 parts of filling Agent. In actual production, when nitrile rubber with different acrylonitrile content is used together with phenolic resin, the higher the acrylonitrile content, the better the physical and mechanical properties of the finished product.
4. Plasticizing system
When nitrile rubber and phenolic resin are used together, the rubber has high stiffness and poor fluidity during molding. It is necessary to add an appropriate amount of plasticizers such as dibutyl phthalate and coumarone resin to give the rubber good fluidity. In actual production, the addition of plasticizer will cause the nitrile rubber compound/phenolic resin tensile strength, fixed elongation strength, abrasion resistance and hardness to decrease, so the amount of plasticizer is generally controlled below 10 parts.
When nitrile rubber, nitrile reclaimed rubber and phenolic resin are used together to produce rubber products, manufacturers can choose the appropriate vulcanization system, filling system, plasticizing system, etc. according to actual needs to further optimize product quality; later editors will continue to share with you Production process skills of nitrile rubber, nitrile reclaimed rubber and phenolic resin together.
Exclusive original article [commercial authorization] reprint, excerpt and excerpt in any form are prohibited without written authorization. Focus on Hongyun rubber: learn the process formula and raw material technology of producing rubber products from recycled rubber to help you reduce costs and increase profits