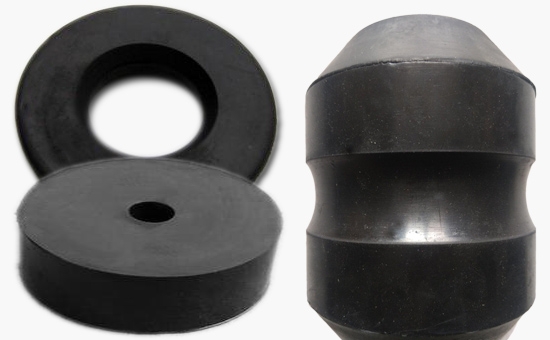
The shock-absorbing material processed from natural rubber as the main raw material has good overall performance, excellent fatigue resistance, low heat generation and small creep during use, and is easy to bond with metal parts. Among them, natural rubber 2LLYY1230 shock-absorbing material with a Shore hardness of 30-40 degrees can be used to prepare rubber springs, rubber bushes, support pads, supports and other ordinary shock-absorbing products. In actual production, reasonable selection of rubber raw materials and rubber additives for low-hardness shock-absorbing materials can further optimize the performance of the finished shock-absorbing products.
1. Commonly used rubber raw materials
In actual production, manufacturers of shock-absorbing products can use natural rubber alone to produce low-hardness shock-absorbing products, or they can use natural rubber together with other types of rubber such as butadiene rubber, latex reclaimed rubber, isoprene reclaimed rubber, etc. A better shock-absorbing material. The use of butadiene rubber in natural rubber can further improve the elasticity, cold resistance and wear resistance of shock-absorbing materials. The indicators of reclaimed latex rubber are basically the same as those of natural rubber, which can effectively reduce the cost of shock-absorbing materials and improve the performance of rubber materials. The use of isoprene reclaimed rubber in natural rubber shock-absorbing materials can not only reduce costs, but also further improve the chemical stability and viscosity of shock-absorbing materials.
2. Commonly used rubber accessories
When natural rubber is used to produce low-hardness shock-absorbing materials, sulfur vulcanization is generally used, with accelerator M, accelerator NOBS, accelerator D/DM and so on. When the low-hardness damping material needs carbon black reinforcement, mixed gas carbon black and semi-reinforced carbon black can be selected. The softening and plasticizing system can use paraffin oil, naphthenic oil, black and white ointment, etc. Generally, the amount of softener in low-hardness shock-absorbing materials using carbon black is large. The use of antioxidant A, antioxidant D, antioxidant H, and antioxidant 4010NA can significantly improve the aging resistance of natural rubber shock-absorbing materials. The specific varieties can be determined in accordance with the processing performance of the rubber and the product index requirements. If necessary, add paraffin in an appropriate amount.
When using natural rubber to produce low-hardness shock-absorbing products, the rubber product manufacturer can use natural rubber alone, natural rubber/butadiene rubber, or natural rubber/reclaimed rubber. Some shock-absorbing materials can also be directly recycled. Rubber (latex reclaimed rubber, isoprene reclaimed rubber, tire reclaimed rubber), significantly reducing the cost of raw materials. Natural rubber low-hardness shock-absorbing materials should pay attention to the production process parameters and specific operating procedures in the actual production process. The editor will have the opportunity to continue discussing with you later.
Exclusive original article [commercial authorization] reprint, excerpt and excerpt in any form are prohibited without written authorization. Focus on Hongyun rubber: learn the process formula and raw material technology of producing rubber products from recycled rubber to help you reduce costs and increase profits