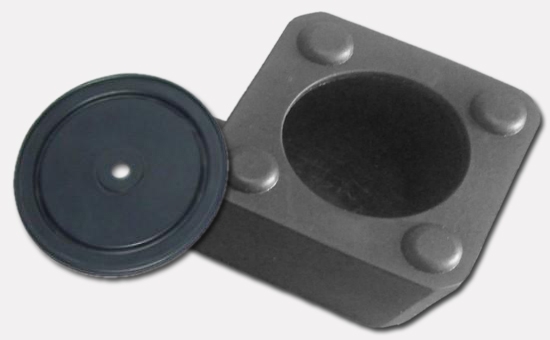
The damage caused by the rapid expansion of cracks or cracks in rubber materials when subjected to force is rubber tearing, which is an important indicator of the resistance of rubber products to damage. In actual production, crystalline natural rubber produces induced crystallization during tearing, which can greatly improve the strain capacity, so the natural rubber itself has a higher tear strength. In actual production, some special products have higher requirements on the tearing performance of natural rubber. What are the factors that affect the tearing strength of natural rubber, and what measures are appropriate?
1. Factors affecting the tear strength of rubber
The type of rubber and the crosslinking density of the vulcanizate are the main factors affecting the tear strength of the vulcanizate. The tear strength of commonly used natural rubber and synthetic rubber decreases sequentially: natural rubber (NR)> isoprene 2YLYY111 rubber (IR)> nitrile rubber (NBR)> butyl rubber (IIR)> neoprene (CR)> butadiene rubber Rubber (BR)> Styrene Butadiene Rubber (SBR)> EPDM (EPDM). Appropriate adjustment of rubber product formula and coordination system can further improve the tear strength of vulcanized rubber.
2. Ways to improve the tear strength of natural rubber
(1) Increasing the cross-linking density of natural rubber vulcanizates can increase the tear strength. The ordinary sulfur vulcanization system of natural rubber products is equipped with a rubber accelerator with medium activity and good flatness. Adjust the amount of vulcanizing agent and accelerator appropriately. Pay attention to vulcanized rubber. The crosslink density is changed to obtain better tear performance. There is an optimal value between tear strength and crosslink density. As the crosslink density increases, the tear strength of the rubber compound increases and a maximum value appears. Continued increase of the crosslink density will cause the tear strength to drop sharply.
(2) When carbon black is used to reinforce natural rubber, increasing the amount of carbon black can increase the tear strength of natural rubber vulcanizate, and a maximum value will appear when the amount increases. When the amount of carbon black continues to be increased, the tear strength of vulcanized rubber will decrease. . The use of isotropic fillers such as carbon black, white carbon black (the use of surface-treated new gas phase white carbon black is better), Bai Yanhua, lithopone powder, zinc oxide, etc., to prepare natural rubber products with higher tear strength ; Anisotropic fillers such as clay and magnesium carbonate are not good for improving the tear strength of vulcanizates.
(3) The use of softening plasticizers will cause the tearing strength of natural rubber vulcanizates to decrease, so the amount of softeners and plasticizers needs to be appropriately reduced.
3. High tear strength natural rubber vulcanized rubber formula
100 parts of natural rubber, 5 parts of zinc oxide, 1 part of stearic acid, 2.5 parts of sulfur, 1.5 parts of accelerator CZ, 55 parts of super wear-resistant carbon black; 165 parts in total. (Vulcanization temperature 140℃, vulcanization time 9min)
When using natural rubber to produce rubber products that require better tear strength, medium and super abrasion-resistant carbon black is generally selected to further improve the tensile strength, tear strength, wear resistance and aging properties of vulcanizates. The editor has the opportunity to continue to share with you other techniques and specific production processes for improving the tear strength of natural rubber vulcanizates.
Exclusive original article [commercial authorization] reprint, excerpt and excerpt in any form are prohibited without written authorization. Focus on Hongyun rubber: learn the process formula and raw material technology of producing rubber products from recycled rubber to help you reduce costs and increase profits