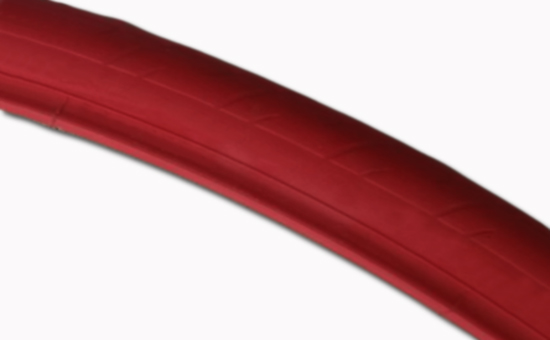
Rubber colorants are substances added in the production of rubber products for the purpose of changing the color of the products. They can be mainly divided into two categories: organic colorants and inorganic colorants; different varieties of colorants have different performance characteristics. When using latex reclaimed rubber to produce colored rubber products, the selection of colorants is very important; a full understanding of the properties of rubber colorants helps to correctly select colorants for colored natural reclaimed rubber products.
1. The tinting strength of rubber colorants
The tinting strength of the rubber colorant is the ability to affect the color of the entire mixture. The greater the tinting strength, the less the amount of colorant and the lower the cost. Generally, the tinting strength of organic pigments 2ELYY831 is larger than that of inorganic pigments; the tinting strength of colorants increases with the decrease of particle size; the tinting strength of colorants can be improved by using color pigments together with white pigments. When selecting colorants for colored latex reclaimed rubber products, the tinting strength of the colorants must be fully considered.
2. Hiding power of rubber colorants
The hiding power of rubber colorants refers to the ability of the colorant to prevent light from penetrating the product, which mainly depends on the difference among the refractive index of the colorant and the reclaimed rubber, the ability to absorb visible light and the particle size; Larger, the better the covering power of the colorant; the stronger the absorption capacity, the better the covering power; the smaller the particle size, the better the dispersion, the higher the covering power, but not less than half of the wavelength of light. In actual production, inorganic colorants have relatively large hiding power and are only suitable for opaque products.
3. Dispersibility of colorants in latex reclaimed rubber
The ideal coloring effect can only be obtained when the colorant is uniformly dispersed in the latex reclaimed rubber with tiny particles. Poor dispersibility of colorants will cause defects such as color difference, uneven coloring, and formation of stripes, which will affect the appearance and physical and mechanical properties of color latex reclaimed rubber products. In actual production, most of the dyes can be dissolved in the latex reclaimed rubber; the pigments are prone to the problem of poor dispersion and can only be used after surface treatment and processing in advance.
In the production of colored latex reclaimed rubber products, if the blue pigment is poorly dispersed, it will turn red; if the green pigment is poorly dispersed, it will turn olive; if the yellow pigment is poorly dispersed, it will turn yellow; if the red color is poorly dispersed, it will turn blue; Poor dispersion of brown and white pigments will cause the product to be yellowish.
4. Heat resistance of rubber colorants
The vulcanization and molding of latex reclaimed rubber products require a long time of thermal processing, and the colorant needs to ensure that no discoloration, fading or sublimation occurs when heated. In actual production, inorganic colorants have better heat resistance than organic colorants; in the production of colored natural reclaimed rubber products, it is necessary to select the appropriate variety of colorants according to the processing temperature.
5. Weather resistance of rubber colorants
When using latex reclaimed rubber to produce colored rubber products that need to be used outdoors for a long time, the weatherability of colorants (including lightfastness and the effect on the weatherability of polymers) needs to be considered. In general, inorganic pigments have better light resistance than organic colorants; among organic colorants, advanced organic pigments such as phthalocyanine, quinacridone, and isoindolinone have good light resistance. Condensed azo type has better weather resistance.
6. Rubber colorant migration resistance
The migration of rubber colorants mainly includes solvent extraction, contact migration and surface ejection. Inorganic pigments are insoluble in polymers, water and organic solvents, and the dispersion in latex reclaimed rubber is heterogeneous and does not cause migration; organic pigments are more prone to migration. When organic pigments are used in color latex reclaimed rubber products, the difficulty of pigment migration has a lot to do with the types of reclaimed rubber and rubber additives, especially plasticizers and softeners.
When using latex reclaimed rubber to produce some colored rubber products, rubber product manufacturers also need to consider the chemical stability and electrical properties of colorants; the editor will continue to share relevant issues with you later.
Exclusive original article [commercial authorization] reprint, excerpt and excerpt in any form are prohibited without written authorization. Focus on Hongyun rubber: learn the process formula and raw material technology of producing rubber products from recycled rubber to help you reduce costs and increase profits