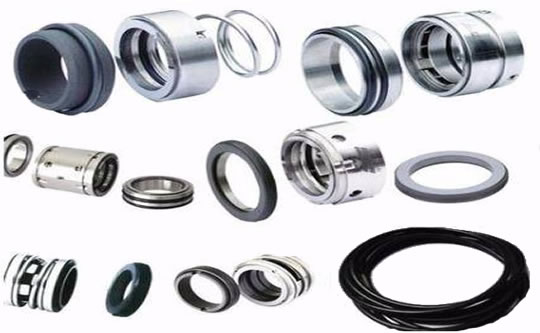
The oil resistance of rubber refers to the ability of rubber vulcanizates to resist oil turbidity. When rubber products and various oils are exposed to a certain temperature range for a long time, the oil may penetrate into the interior of the product, causing volume increase and swelling. At the same time, some soluble agents (mainly low molecular weight plasticizers) may be extracted from the products, resulting in reduced volume (shrinkage). The two is a dynamic balance process. The degree of swelling or shrinkage usually increases with the increase of the contact time between the product and the oil until the volume changes reach equilibrium. The higher the temperature, the shorter the time needed to achieve the volume balance. In addition, some additives in oil may react with rubber molecules, resulting in cross-linking or degradation of rubber.
The comparison test of rubber oil resistance is usually conducted by comparing ASTM standard test oil, and the results are universal and comparable. The viscosity, aniline point and flash point of the standard test oil are specified. The vulcanizate samples were soaked in a certain temperature, and the change rate of volume, hardness, tensile strength and elongation at break or retention rate were measured before and after soaking. For some special products, it is necessary to observe the physical and mechanical properties of the vulcanizate by soaking in certain temperature conditions and measuring the physical and mechanical properties of the vulcanizate. The appearance of the soaked samples, the color of the oil after soaking and the change of the internal composition of the oil products are observed when necessary.
The oil resistance of rubber is usually referred to as non polar oil (fuel, mineral oil, synthetic lubricant). When designing the formulation of oil resistant rubber, we should first understand the composition of the oil medium. The common oil products are as follows:
1. Fuel oil. Ordinary gasoline is a common breed. According to the requirements of environmental protection, the amount of lead in gasoline is reduced, the octane number of gasoline is increased, methanol or ethanol is added to gasoline, or methyl tert butyl ether is added to the gasoline, or the content of aromatic compounds is added, and the mixed fuel oil (polar increase) is obtained, or the peroxide fuel oil is added to the fuel oil. It will accelerate the damage of the vulcanizate.
2. Mineral oil. Mineral oils belong to nonpolar oils. ASTM 1, 2 and 3 are commonly used in this category.
3. Synthetic lubricants. The general synthetic lubricant consists of two parts, the basic liquid and the additive. The types of basic liquids include synthetic hydrocarbons, polyalkyl diols, organic esters, phosphates, silicon containing, fluoro organic compounds, aromatic ethers, water based flame retardant liquid chlorinated hydrocarbons, etc. the additives include antioxidants, corrosion inhibitors, detergents / dispersants, viscosity index modifiers and pour point inhibitors, foam agents, and extreme pressure agents. Wait.
Additives for general synthetic lubricants are mainly used to improve the physical and chemical properties of various basic liquids. Most chemical additives are more reactive than basic liquids and have greater chemical attack on rubber. Therefore, rubber products working in synthetic lubricants not only resist the action of basic liquids, but also resist the erosion of additives in synthetic lubricants. Therefore, synthetic lubricants are far more complex and harsh to rubber erosion than fuel oil and mineral oil. There are many kinds of oil products, their composition is different, chemical properties are distinctly different, polarity is very far, or polarity is strong, or non polar, or neutral, which makes the choice of rubber brand difficult. The double bond of unsaturated rubber is more, the additive in the synthetic oil, such as sulfur and phosphorus additive, some detergent and superhigh pressure additive will make the rubber surface seriously harden.
During the contact process of rubber products and oil products, the temperature may change obviously, such as the change from low temperature to high temperature. Therefore, in many cases, in addition to considering the oil resistance of rubber, the high and low temperature resistance of rubber must also be considered. The oil resistance of rubber is closely related to heat resistance and cold resistance. Generally, the oil resistance of general rubber is improved, and its heat resistance will also increase, but its cold resistance will often decrease. The more strongly polar components in polar rubber, the greater the intermolecular force, the increase of oil resistance and the increase of heat resistance, however, the Tg of rubber also increases, and its cold resistance decreases. For example, the cold resistance of FPM is poor, but its oil resistance and heat resistance are the best. VMQ has the best cold resistance and good heat resistance, and its oil resistance is poor. FVMQ has good oil resistance, heat resistance and cold resistance. Therefore, the selection of rubber should take into consideration the variety and composition of the oil, oil resistance, heat resistance, cold resistance, basic physical and mechanical properties, and the choice of rubber when necessary.
Varieties of oil resistant rubber include: FPM, FVMQ, ACM, AEM, HNBR, NBR, CO, ECO, CSM, CR, etc. NR, IR, BR, SBR, IIR and EPDM are non oil resistant rubber.
NBR is a commonly used oil resistant rubber, and its oil resistance increases with the increase of acrylonitrile content. NBR with high acrylonitrile content is resistant to mineral oil, but its heat resistance is limited. When the oil temperature exceeds 150 degrees, HNBR, FPM, FVMQ or ACM should be used. However, the price of FPM and FVMQ is very high, and it can be used in FPM with less than 50% ACM to reduce the cost of the compound. The heat resistance of ACM is much better than that of NBR. ACM can work 1000h in ASTM3 oil at 177 C.
Exclusive original article [commercial authorization] reprint, excerpt and excerpt in any form are prohibited without written authorization. Focus on Hongyun rubber: learn the process formula and raw material technology of producing rubber products from recycled rubber to help you reduce costs and increase profits