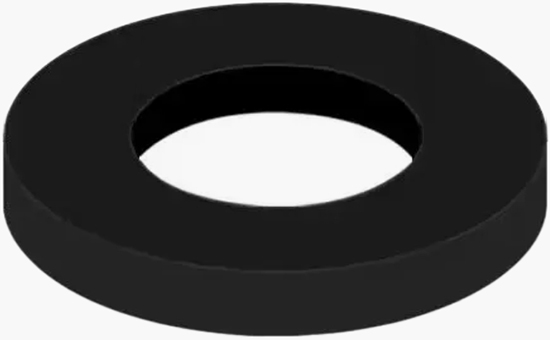
High-hardness oil-resistant and shock-absorbing rubber products processed from nitrile butadiene rubber as the main raw material, such as shock absorbers and gaskets, can maintain good performance for a long time when used in oil media, can maintain stable performance, and are not easy to expand, soften or rupture. The use of reclaimed rubber in rubber products is an effective means to improve economic benefits; So can reclaimed rubber be mixed in the formula of high-hardness nitrile oil-resistant shock-absorbing rubber compound? What issues should be considered when using reclaimed rubber to reduce costs for oil-resistant and shock-absorbing rubber products?
1. Consider whether the reclaimed rubber meets the needs of nitrile shock-absorbing rubber for oil resistance
The blending of reclaimed rubber may affect the oil resistance of nitrile rubber; Therefore, when mixing reclaimed rubber in high-hardness nitrile oil-resistant shock-absorbing rubber products, it is necessary to evaluate the oil resistance of the reclaimed rubber and ensure that the finished product meets the requirements of oil resistance. Nitrile reclaimed rubber retains the basic performance characteristics of nitrile rubber, oil resistance, wear resistance and aging resistance, and is an ideal raw material for replacing nitrile rubber to produce high-hardness oil-resistant shock-absorbing rubber.
In actual production, 10-30 parts of nitrile reclaimed rubber mixed with high-hardness nitrile rubber shock-absorbing rubber can improve the aging resistance of the finished product while ensuring the oil resistance of the rubber compound, reduce expansion and contraction, and dimensional stability.
2. Consider the hardness and strength of reclaimed rubber on the hardness and strength of nitrile oil-resistant and shock-absorbing rubber
High-hardness nitrile oil-resistant shock-absorbing rubber products have high requirements for rubber hardness, and the hardness of some products needs to reach more than 90 degrees (Sauer hardness); Therefore, when mixing reclaimed rubber to reduce oil resistance and shock absorption rubber, we must fully consider the hardness change of the rubber material after mixing with reclaimed rubber. Reclaimed rubber may reduce the hardness and strength of the product, and it is necessaryE4LYY229 to determine the appropriate proportion of reclaimed rubber through experiments to maintain the required physical properties; Generally, nitrile reclaimed rubber with high rubber content has higher mechanical strength.
3. Consider the quality uniformity of reclaimed rubber
When using reclaimed rubber to reduce the cost of high-hardness nitrile oil-resistant shock-absorbing rubber products, it is necessary to strictly control the quality of reclaimed rubber to ensure that its performance is stable and meets the requirements; Batch-to-batch variation in reclaimed rubber may affect the consistency of product quality and requires strict quality inspection and control. It is recommended that rubber products manufacturers directly cooperate with regular reclaimed rubber factories, with large output, sufficient inventory, and a winning quality control system, so that product quality is more stable.
4. Consider the processing technology performance of nitrile rubber/reclaimed rubber and use rubber to produce oil-resistant and shock-absorbing rubber
The processing properties of reclaimed rubber are different from those of new rubber, so when using nitrile rubber and reclaimed rubber together to produce high-hardness, oil-resistant, shock-absorbing rubber compounds, it is necessary to adjust the processing temperature and time (mixing and vulcanization) to ensure uniform mixing and vulcanization. In general, the rubber mixed with recycled rubber has better fluidity, and the heat generation of mixing, hot mixing, extrusion, calendering and other materials is lower than that of pure raw rubber rubber, which is conducive to avoiding scorching due to high rubber temperature.
In addition, the addition of reclaimed rubber will affect the rate and degree of vulcanization, and the vulcanization system needs to be adjusted to ensure that the product achieves the desired vulcanization characteristics.
Nitrile oil-resistant shock-absorbing rubber products mostly use nitrile reclaimed rubber, which can better ensure the oil resistance of the product while reducing costs. When nitrile rubber/nitrile reclaimed rubber is used together to produce oil-resistant and shock-absorbing rubber products, it is also necessary to adjust the formula appropriately, especially the vulcanization system and reinforcing system, carry out the necessary reliability tests, verify the performance and life of oil-resistant rubber after mixing with reclaimed rubber, and ensure that the products mixed with reclaimed rubber meet the requirements of safety standards and regulations. Subsequently, we will share with you the key points of formula design and vulcanization formula of nitrile rubber and nitrile reclaimed rubber to produce high-hardness, oil-resistant and shock-absorbing rubber products.
Exclusive original article [commercial authorization] reprint, excerpt and excerpt in any form are prohibited without written authorization. Focus on Hongyun rubber: learn the process formula and raw material technology of producing rubber products from recycled rubber to help you reduce costs and increase profits