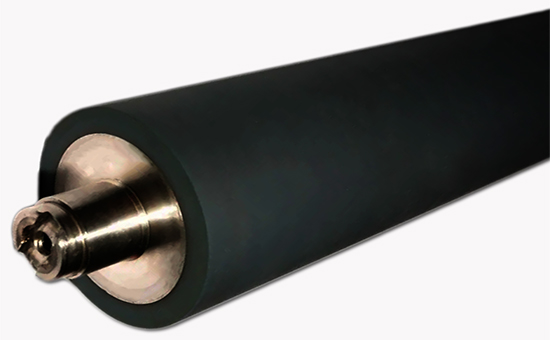
Nitrile reclaimed rubber has a large oil resistance coefficient, wear resistance and anti-aging. It can replace high-priced nitrile raw rubber to produce various rubber products, effectively reducing the cost of raw materials. The rubber roller is made of metal and other materials as the core and covered with rubber vulcanized. The rubber roller used in printing, printing and dyeing, chemical fiber, plastic and other equipment needs to be in contact with oil medium or aliphatic hydrocarbon solvent for a long time. Generally, nitrile rubber is used as the core. The main raw materials are processed; nitrile reclaimed rubber can be used alone or in combination with nitrile rubber to produce the above rubber rollers; rational design of the formula can reduce more costs on the premise of ensuring the quality of the rubber rollers.
1. How to correctly select rubber material for nitrile reclaimed rubber production cots
When using nitrile reclaimed rubber as the main rubber raw material to produce rubber rollers, it is recommended to use reclaimed rubber products that are close to the technical specifications of the rubber rollers. In actual production, the top rubber of the rubber roller has certain requirements on mechanical properties such as hardness, tensile strength, elasticity, etc., especially the hardness and rubber content.
In order to ensure the smooth forming of the rubber roller, the rubber material needs to have a high rubber content, so it is recommended to use nitrile reclaimed rubber with a high rubber content. If the hardness of the rubber roller is not suitable, it is difficult to achieve the ideal use effect; therefore, when selecting the nitrile reclaimed rubber 2ELYY519 for rubber rollers, we must fully consider various parameters such as the hardness of the rubber, and adjust the vulcanization system, reinforcement system, and softening system. Compounding agent to prepare rubber roller products with suitable hardness.
2. Design skills of rubber roller vulcanization system for nitrile reclaimed rubber production
When using nitrile reclaimed rubber to produce rubber rollers, a sulfur-accelerator system is generally used; with zinc oxide, the thermal conductivity of the rubber can be further increased. The hardness of vulcanizate is related to the crosslinking density, the greater the crosslinking density, the higher the hardness. Therefore, increasing the amount of sulfur in the formula of the nitrile reclaimed rubber roller can increase the hardness of the rubber. Generally, when the hardness of nitrile reclaimed rubber is 65 degrees (Shore hardness A), the amount of sulfur is about 4-5 parts; when the hardness of the rubber roller is above 80 degrees, the amount of sulfur will even exceed 20 parts.
3. Design skills of rubber roller reinforcement system for nitrile reclaimed rubber production
Reinforcing agents and fillers are indispensable in the formulation of rubber rollers produced with nitrile reclaimed rubber as the main raw material; generally, with the increase in the amount of reinforcing agents and fillers, the hardness of the rubber material increases. In actual production, the commonly used reinforcing agent for nitrile reclaimed rubber rollers is semi-reinforced carbon black, and an appropriate amount of white carbon black can also be added; light calcium, talc, and hard clay are commonly used as fillers. The amount of reinforcing agent and filler in the nitrile rubber roller should not be too much, otherwise the self-adhesion of the rubber material will be poor, and problems such as difficulty in laminating the film and delamination during production will easily occur.
When increasing the hardness of nitrile reclaimed rubber rollers by increasing the dosage of reinforcing agents and fillers, rubber product manufacturers also need to fully consider the hardness of nitrile reclaimed rubber itself. Taking semi-reinforced carbon black as an example, the initial hardness of the reclaimed rubber + 1/3 × parts is the hardness of the nitrile rubber roller.
4. Design skills of rubber roller softening system for nitrile reclaimed rubber production
When using nitrile reclaimed rubber to produce rubber rollers, a certain self-adhesion is the basis for ensuring the smooth forming of the rubber roller. The softening system uses an appropriate amount of rosin and pinene resin with good tackifying effect to facilitate the forming operation of the rubber roller. When nitrile reclaimed rubber is used to prepare low-hardness rubber rollers such as printing rubber rollers, the hardness can be adjusted by adjusting the type and amount of softener; avoid using varieties that are not easily drawn out by ink, otherwise the hardness of the surface rubber of the nitrile reclaimed rubber roller will increase. , size shrinkage and other issues, affecting the normal use of the product.
5. Design skills of nitrile reclaimed rubber production rubber roller anti-aging system
Anti-aging agent RD, anti-aging agent AH, anti-aging agent MBH, etc. are often used in the production of nitrile reclaimed rubber rollers. If necessary, a variety of anti-aging agents can be used in combination.
In actual production, nitrile reclaimed rubber can be used alone in the production of nitrile rubber rollers, or nitrile reclaimed rubber and nitrile rubber can be used together; rational design of formula, appropriate adjustment of production procedures and process parameters can further improve the finished product. Quality; in the later stage, the editor will continue to share with you the production process of nitrile reclaimed rubber rollers and the problems that need attention in production.
Exclusive original article [commercial authorization] reprint, excerpt and excerpt in any form are prohibited without written authorization. Focus on Hongyun rubber: learn the process formula and raw material technology of producing rubber products from recycled rubber to help you reduce costs and increase profits