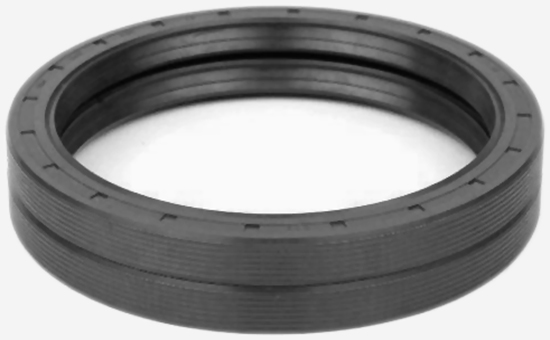
Nitrile rubber and nitrile reclaimed rubber have a large oil resistance coefficient and are widely used in the production of oil-resistant rubber products. They can maintain good performance when used in oil media for a long time. Nitrile rubber contains polar nitrile groups, the cohesive energy among macromolecules is larger than non-polar rubber, the viscosity is higher, and the processing performance is poor. It is necessary to add softeners and plasticizers to reduce the viscosity of the rubber and improve the plasticity. Improve process performance. In actual production, the type and amount of plasticizer directly affect the oil resistance of nitrile rubber, and manufacturers of high oil resistance nitrile rubber products should choose carefully.
1. Commonly used plasticizers for nitrile rubber products
Rubber plasticizers can reduce the intermolecular forces, and then lower the glass transition temperature of the rubber, improve the plasticity and fluidity of the rubber compound, and provide a better foundation for subsequent molding operations such as calendering and extrusion. In actual production, ester compounds and ether compounds have similar polarities with nitrile rubber and have good compatibility with nitrile rubber. They are commonly used plasticizers in the production of nitrile rubber products.
2. Reasons why plasticizers affect the oil resistance of nitrile rubber
The reason why plasticizers affect the oil resistance of nitrile rubber is related to the difficulty of being extracted by petroleum solvents in nitrile rubber or nitrile reclaimed rubber. The degree of extraction depends on the molecular structure of the plasticizer. The linear structure containing alkyl 2YLYY123 is easy to extract, and the more polar plasticizers such as phenyl and ester groups are more difficult to extract. It should be noted that if the alkyl straight chain contains more branched chains, the diffusion of plasticizer molecules can be reduced, and it will show better oil resistance.
In addition, the cold-resistant plasticizer is easily extracted in the oil, and the oil resistance performance is reduced; it can be seen that the influence of the plasticizer on the cold resistance and oil resistance of nitrile vulcanizates is contradictory and needs to be considered comprehensively.
3. Plasticizer suitable for high oil-resistant nitrile rubber products
In actual production, butyl benzyl phthalate (BBP), tricresyl phosphate and dinonyl phthalate (DNP) are all oil-resistant plasticizers. Manufacturers of high oil-resistant nitrile rubber products can consider These products. Polyester plasticizers have a large molecular weight, very high temperature for solvent extraction, low volatility and low permeability, but are not ideal for cold resistance, plasticization and compatibility with rubber. Therefore, high oil resistance rubber products are especially suitable for cold resistance. Polyester plasticizers should not be used for rubber products with high performance requirements.
In the production of nitrile rubber products, choosing a suitable plasticizer will not plasticize the rubber, and can also improve the elasticity and cold resistance of nitrile vulcaniz To improve the plasticity, fluidity, etc. of the rubber compound, many manufacturers of high oil-resistant nitrile rubber products choose to use nitrile reclaimed rubber in the formula to reduce the cost and improve the performance of the rubber compound.
In order to further improve the processing performance and adhesion of high oil-resistant nitrile rubber products, rubber product manufacturers can also use chlorinated paraffin, fatty acid, ointment, coumarone, coal coke resin, liquid nitrile, etc., with plasticizers, Improve the performance of high oil-resistant nitrile rubber products; later editors will have the opportunity to continue discussing related issues with you.
Exclusive original article [commercial authorization] reprint, excerpt and excerpt in any form are prohibited without written authorization. Focus on Hongyun rubber: learn the process formula and raw material technology of producing rubber products from recycled rubber to help you reduce costs and increase profits