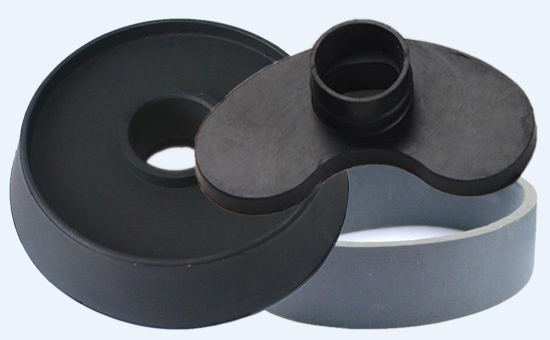
Nitrile rubber has excellent oil resistance. The processed oil-resistant rubber products can be used for a long time in oil media and are not prone to swelling problems. In actual production, many nitrile and oil-resistant rubber products need to work under high temperature conditions. Can nitrile rubber meet this demand? How to design formula when using nitrile rubber to produce oil-resistant and high-temperature resistant rubber products? The editor today shares with you a high-temperature nitrile and oil-resistant compound formula.
1. Reference formula
100 parts of nitrile rubber, 5 parts of zinc oxide, 1 part of stearic acid, 1.5 parts of antioxidant, 0.5 parts of sulfur, 1 part of accelerator CZ, 2 parts of accelerator TT, 50 parts of semi-reinforcing carbon black, high wear-resistant carbon 14 parts of black, 11 parts of rubber oil; total: 186 parts. Formula curing conditions: curing conditions: 155℃×23min.
2. Formula design
(1) Rubber raw materials: When nitrile rubber is used to prepare high-temperature oil-resistant rubber compounds, nitrile rubber with high acrylonitrile content is generally selected, which has better oil resistance and high temperature resistance. When using nitrile reclaimed rubber to reduce the production cost of high temperature resistant and oil resistant nitrile products 2YLYY318, choose products that are closer to the index requirements of oil resistant and high temperature resistant products, and more parts of nitrile reclaimed rubber can be used to effectively reduce the cost of raw materials.
(2) Curing system: Low-sulfur-thiuram curing system is generally selected for high temperature and oil-resistant nitrile rubber, and the cross-linked network structure formed by the vulcanized rubber has good heat resistance stability. In practical applications, the high temperature oil environment will cause the physical properties of rubber products to decline, so the cross-linked network with good heat resistance stability is very important.
(3) Reinforcement system: The tensile strength of nitrile rubber after vulcanization with low-sulfur-thiuram system is lower than that of sulfur vulcanized rubber. Therefore, product manufacturers generally choose to use both high wear-resistant carbon black and semi-reinforced carbon black. Better adjust the relationship between the high temperature resistance and tensile strength of the rubber compound. Semi-reinforcing carbon black has dual functions of reinforcement and filling, which can give the rubber compound high elongation, low heat build-up, high elasticity and good aging resistance; high wear-resistant carbon black can significantly improve the stretch of nitrile rubber Strength, tear strength, wear resistance, etc.
(4) Softening system: When designing a softening system for high-temperature oil-resistant nitrile rubber, attention should be paid to the expansion and contraction of the network structure due to the swelling of the impregnating oil and the extraction of the operating oil. When selecting rubber oil varieties, the diffusion and migration between the internal operating oil and the medium oil of the nitrile vulcanizate should be minimized.
When using nitrile rubber or nitrile rubber/reclaimed rubber to produce oil-resistant and high-temperature-resistant rubber products, rubber product manufacturers also need to strictly control the production process, especially mixing and vulcanization, and pay attention to the setting of various process parameters. Edit to continue discussing with you.
Exclusive original article [commercial authorization] reprint, excerpt and excerpt in any form are prohibited without written authorization. Focus on Hongyun rubber: learn the process formula and raw material technology of producing rubber products from recycled rubber to help you reduce costs and increase profits