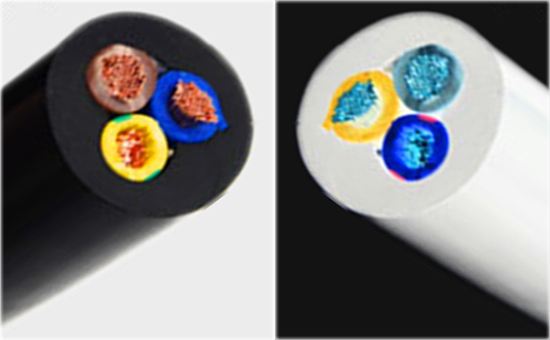
EPDM rubber and EPDM reclaimed rubber have excellent resistance to high and low temperature, weather resistance and aging resistance. They are ideal materials for producing indoor and outdoor cable sheaths. Currently, the color of cable sheaths on the market is various. The user's later maintenance and repair provides convenience; then in actual production, how are the different colors of the cable sheath produced? What are the differences between EPDM cable skin formulations?
Xiaobian today uses the black cable sheath and white cable sheath as an example to talk about the difference in the EPDM wire and cable skin recipe for different colors.
In the cable sheathing formula with EPDM as the main raw material, the black cable sheathing formula is generally combined with sulfur, zinc oxide, accelerator TMTD, stearic acid, semi-reinforcing carbon black and a certain proportion of rubber oil. The white EPDM wire and cable sheath formulation is combined with sulfur, zinc oxide, accelerator TMTD, stearic acid, ultrafine calcium carbonate and a certain proportion of rubber oil. We can see that from the point of view of the compounding agent, the black and white two-color wire and cable sheath formulation is different in the type of reinforcing filler.
Carbon black is the most used reinforcing agent in the rubber product industry. It can give the rubber material a good processing technology and physical and mechanical strength in the formulation of rubber products. The EPDM rubber filled with semi-reinforcing carbon black has high elongation at break. High elasticity, low heat generation and excellent aging resistance, it is a common reinforcing agent for black EPDM rubber cable sheath; but for white EPDM cable sheath, black powdery carbon black is undoubtedly cable sheath Color matching brings a lot of trouble; this time you may wish to try ultra-fine calcium carbonate.
Calcium carbonate is the most commonly used rubber filler in the rubber products industry. Ultrafine calcium carbonate is a calcium carbonate and white powder with a primary particle size of 0.02-0.1 μm. It has good wettability and reinforcement to rubber. The toughening effect and reinforcing effect of the treated ultra-fine calcium carbonate in the EPDM compound are more remarkable, so it can replace the carbon black as the “Bai Yanhua” in the white EPDM cable sheath formulation; the rubber product manufacturer can also The use of an appropriate amount of silica in the light-colored EPDM cable skin coating provides a good basis for coloring the cable sheath.
When using EPDM rubber to produce wire and cable sheaths of different colors, be sure to choose suitable rubber materials and reinforcing fillers. The dark and black cable sheaths can also be used with appropriate amount of black EPDM reclaimed rubber. Production cost; it is best not to use EPDM reclaimed rubber in the white EPDM cable sheath. Light gray EPDM reclaimed rubber is a good choice.
Exclusive original article [commercial authorization] reprint, excerpt and excerpt in any form are prohibited without written authorization. Focus on Hongyun rubber: learn the process formula and raw material technology of producing rubber products from recycled rubber to help you reduce costs and increase profits