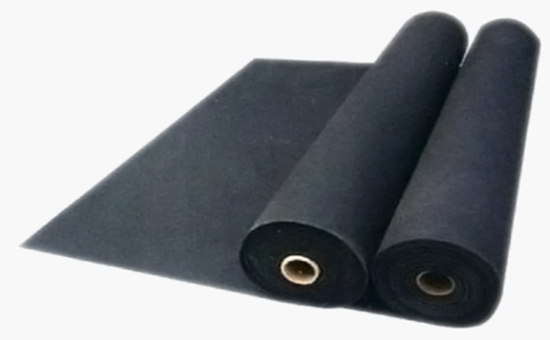
The quality of waterproof membranes on the market is different. The waterproof membranes made of EPDM and butyl rubber are of good quality, especially EPDM waterproof membranes, which have excellent weather resistance. Ozone resistance, heat resistance, chemical stability, good waterproof effect and long service life; however, the price of EPDM rubber is high, and the appropriate amount of EPDM reclaimed rubber in EPDM waterproofing membrane has become the majority of rubber products manufacturers. Commonly used processing methods. EPDM reclaimed rubber is a kind of rubber compound processed from waste ethylene-propylene rubber products. If it is used improperly, it will directly affect the performance and service life of EPDM waterproofing membrane. How to better use EPDM reclaimed rubber to reduce waterproofing coil Material production costs?
1. Formulation technique for using EPDM reclaimed rubber and original rubber
When using EPDM reclaimed rubber and EPDM rubber to produce waterproof membranes, it is first necessary to select an EPDM reclaimed rubber that is the closest to the requirements of waterproof membranes for rubber product formulation; design reclaimed rubber/original rubber When using the waterproofing membrane vulcanization system, the accelerator M, the accelerator BZ, the accelerator ZDC, and the accelerator TMTD are used together; the amount of carbon black is increased and the amount of calcium carbonate is reduced; and a small amount of tall oil is added to the formula to replace the other softening oil. Improve the tensile strength and elongation at break of EPDM waterproofing membranes.
2, EPDM reclaimed rubber and original rubber combined with mixing techniques
The feeding timing and mixing sequence of the ternary regenerated rubber and the EPDM rubber in the mixing process will also affect the physical index of the EPDM waterproofing membrane. There are two main mixing processes commonly used by rubber manufacturers: the EPDM reclaimed rubber and the EPDM rubber are evenly mixed, then the compounding agent is added, or the blended EPDM rubber is vulcanized. After the EPDM reclaimed rubber is mixed evenly. The test shows that: EPDM rubber and EPDM reclaimed rubber are added to the internal mixer (the rubber compound after mixing with the reclaimed rubber is better). After mixing for 2-3 minutes, the mixture is evenly mixed. Then add various small materials, large materials, and rubber discharge according to the general procedure, and the rubber material has higher tensile strength, higher elongation and better tear strength.
Reasonable formula design and correct process operation are the basis for ensuring the quality of EPDM waterproofing membrane. The production of waterproofing membrane with EPDM reclaimed rubber/original rubber can reduce the cost of raw materials and improve to a certain extent. And rubber processing technology performance; rubber products manufacturers can choose the appropriate EPDM reclaimed rubber according to their own needs and national standards, design a reasonable waterproof coil formulation, to achieve a win-win quality and cost.
Exclusive original article [commercial authorization] reprint, excerpt and excerpt in any form are prohibited without written authorization. Focus on Hongyun rubber: learn the process formula and raw material technology of producing rubber products from recycled rubber to help you reduce costs and increase profits