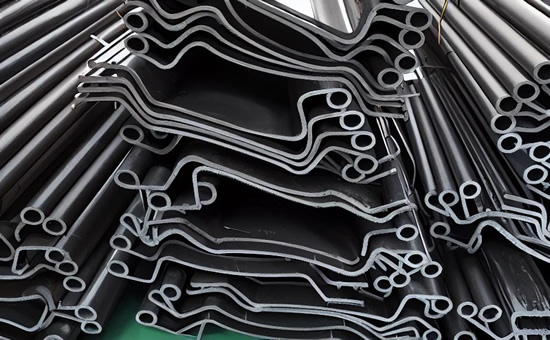
Sound barrier elastic rubber mat is a kind of rubber products installed on the sound barrier system to reduce noise transmission, the role is to improve its sound insulation effect, EPDM rubber, natural rubber, neoprene, butyl rubber, nitrile rubber, etc. can be used to produce sound barrier elastic rubber pads. EPDM reclaimed rubber retains the good heat resistance, weather resistance and corrosion resistance of EPDM original rubber, and can replace EPDM rubber to produce sound barrier elastic rubber pads, which can be used alone or in combination with other rubbers to effectively reduce the cost of raw materials.
Compared with EPDM rubber, EPDM reclaimed rubber not only has the basic performance characteristics of EPDM original rubber, but also has a much lower price than original rubber; Therefore, the use of EPDM reclaimed rubber to produce sound barrier elastic rubber pads can effectively reduce the cost of raw materials; In addition, EPDM reclaimed rubber has the characteristics of good plasticity, low power consumption, easy film output and compression, stable plasticity, etc., and better processing performance.
The general vulcanization process of EPDM reclaimed rubber for the production of sound barrier elastic rubber pads mainly includes raw material preparation, mixing, extrusion or calendering, vulcanization, etc.
1. Prepare raw materials: When EPDM reclaimed rubber produces sound barrier elastic rubber pads, it is first necessary to determine the formula ratio of EPDM reclaimed rubber, and choose peroxide or sulfur vulcanization according to actual needs; Use carbon black or white carbon black to enhance the mechanical properties of rubber; Paraffin oil and ester oil are selected as softeners to improve the processing performance and flexibility of reclaimed rubber; Use antioxidants in an appropriate amount to improve the aging resistance of rubber.
2. Mixing: Mix EPDM reclaimed rubber and various compounding agents in the open mill or internal mixer. Attention should be paid to temperature control during the mixing process to avoid excessive temperature leading to rubber degradation.
3. Extrusion or calendering: The mixed rubber material is molded into the desired shape by an extruder or calender.
4. Vulcanization: Put the formed EPDM reclaimed rubber products into the vulcanization machine for vulcanization. According to the thickness of the product and the required properties, set the appropriate vulcanization temperature and time.
5. Post-treatment: After vulcanization, EPDM reclaimed rubber sound barrier elastic rubber mat needs to be trimmed, cleaned and other post-treatment processes to remove excess leftovers and mold release agents.
The design and manufacture of sound barrier elastomeric rubber mats requires a combination of factors to ensure their performance and effectiveness in real-world applications. The sound barrier elastic rubber mat produced by high-quality EPDM reclaimed rubber has good elasticity, weather resistance, sound insulation, abrasion resistance, aging resistance, etc., and is widely used in outdoor sound barrier systems; It can not only improve economic benefits, but also solve the problem of waste rubber pollution.
Exclusive original article [commercial authorization] reprint, excerpt and excerpt in any form are prohibited without written authorization. Focus on Hongyun rubber: learn the process formula and raw material technology of producing rubber products from recycled rubber to help you reduce costs and increase profits