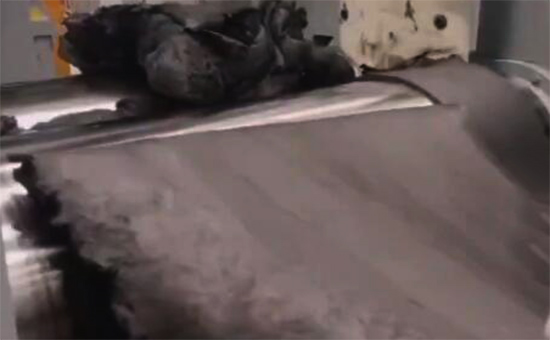
The open type rubber mixing machine is one of the important rubber mixing equipment in the rubber product industry, which can be used for plastic refining, mixing, tablet pressing, hot refining, rubber supply, rubber breaking, as well as crushing, kneading and refining of recycled rubber. When using ethylene propylene diene monomer recycled rubber or ethylene propylene diene monomer rubber/recycled rubber blends to produce rubber products, the mixing process can be carried out in the open mill; What are the key operation points to be mastered when mixing EPDM reclaimed rubber in the open mill?
1. Open mill mixing process of ethylene propylene diene monomer recycled rubber
When the EPDM reclaimed rubber is mixed on the open mill, first open enough cooling water, reduce the roll pitch, put in EPDM reclaimed rubber, and break the rubber; After forming continuous roll covering glue, small materials such as zinc oxide and stearic acid are added; Then slowly add some fillers, such as carbon black; Gradually increase the roll pitch, add the remaining filler 2ELYY1111 and oil, and be careful with the cutter when the material is basically mixed to make it fully dispersed; Finally, vulcanizing agent and accelerator are added; After mixing evenly, thin the tube for several times.
When mixing EPDM recycled rubber in the open mill, the flow of rubber material among the rollers is laminar flow, and the rubber material is mixed according to the laminar flow rule after the addition of the mixture, which is always limited to a certain range; It is necessary to change the flow direction of the rubber material by cutting, triangulating, rolling, twisting or overturning to ensure that the rubber material is mixed evenly. Compared with EPDM raw rubber, EPDM reclaimed rubber has better fluidity.
2. Precautions for mixing EPDM recycled rubber with open mill
(1) When ethylene propylene diene monomer recycled rubber is used together with ethylene propylene diene monomer rubber with poor viscosity, it is not easy for ethylene propylene rubber to roll on the open mill. It is recommended to adopt small roll spacing for mixing. After continuous roll wrapping of raw rubber, start feeding as soon as possible.
(2) The oil and powder used in ethylene propylene diene monomer recycled rubber products need to be added in batches. If there is powder or oil that has not been eaten, be careful with the cutter, otherwise it will cause roll off.
(3) The feeding sequence of ethylene propylene diene monomer recycled rubber during mixing on the open mill is: ethylene propylene diene monomer recycled rubber → reinforcing filler (such as carbon black), zinc oxide and stearic acid → operating oil and non reinforcing filler → accelerator and curing agent.
(4) When EPDM reclaimed rubber is mixed in the open mill, the open mill temperature is generally controlled at 50-70 ℃; The use of high reinforcing filler in the vulcanization formula of EPDM reclaimed rubber must pay attention to the cooling of the drum because of its large heat generation.
(5) When EPDM reclaimed rubber is mixed in the open mill, the rubber material tends to "preferentially" wrap a roll, or wrap the front roll
The rear roll may be wrapped. The best way is to operate on the roll on which the rubber is wrapped. Don't waste time by trying to transfer the rubber from the wrapped roll to the other roll.
When EPDM reclaimed rubber is mixed in the open mill, the quality of the mixed rubber directly affects the service performance and life of EPDM reclaimed rubber products. Later, Xiaobian will continue to share with you other issues that need attention when mixing EPDM reclaimed rubber in the open mill.
Exclusive original article [commercial authorization] reprint, excerpt and excerpt in any form are prohibited without written authorization. Focus on Hongyun rubber: learn the process formula and raw material technology of producing rubber products from recycled rubber to help you reduce costs and increase profits