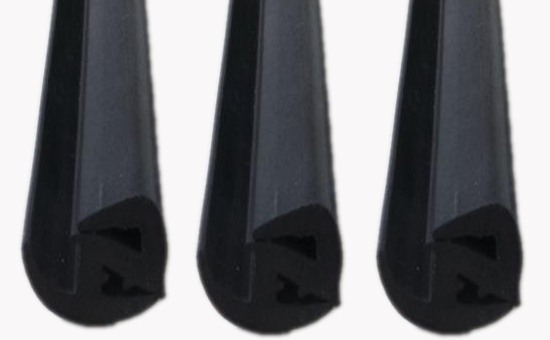
EPDM rubber sealing strip has good ozone resistance and aging resistance. It is mostly used for sealing doors and windows of vehicles and buildings, and maintains a good sealing effect for a long time. In actual production, many EPDM sealing strips use different proportions of EPDM reclaimed rubber, which effectively reduces the cost of raw materials; adjusting the formula of EPDM rubber sealing strips containing reclaimed rubber can further optimize the comprehensive performance of the sealing strip and extend it Product life.
1. EPDM sealing strip physical requirements
EPDM rubber seals require the rubber to have weather resistance and ozone aging resistance to ensure the performance and life of the seal; the rubber is required to have the characteristics of good compression and permanent deformation and good cold resistance. 2YLYY427, in high and low temperatures It has good sealing performance under the conditions; it requires excellent rubber extrusion process performance. When using EPDM reclaimed rubber to produce rubber sealing strips, choose ethylene propylene reclaimed rubber with high rubber content and high fineness as much as possible to better ensure the production efficiency of the sealing strip and the performance of the finished product.
2. EPDM sealing strip matching system
When using EPDM reclaimed rubber to reduce the raw material cost of rubber sealing strips, you can use EPDM virgin rubber and EPDM reclaimed rubber together, or EPDM rubber and neoprene, natural rubber or styrene butadiene rubber together to further improve Rubber material process performance. The anti-aging agents 4010NA, RD, AW and other chemical anti-aging agents commonly used in anti-aging systems are used together with paraffin to further improve the ozone aging resistance and oxygen resistance of the sealing strip. In the softening system, paraffin oil, naphthenic oil and other products that are not easy to volatile and migrate are used.
3. Special additives for EPDM sealing strips
In actual production, to improve the stiffness and appearance quality of the rubber material used in EPDM sealing strips, an appropriate amount of ointment or low molecular polyethylene can be added to the softening system. When using EPDM reclaimed rubber to produce solid sealing strips, adding 5-10 parts of water absorbing agent such as zinc oxide can further improve the extrusion performance of the rubber; in actual production, choose calcium oxide with a particle size of more than 400 mesh , When used, it should be made into a paste with oils and then added to the rubber.
The production of rubber sealing strips with EPDM reclaimed rubber as the main raw material generally uses a common sulfur-accelerator vulcanization system, with a suitable amount of zinc oxide and stearic acid; the reinforcing filling system mostly uses semi-reinforcing carbon black and fast pressing black. Choose talcum powder, calcium carbonate filling, not detailed here. Later, the editor will have the opportunity to continue discussing with you the related issues of using EPDM reclaimed rubber to produce rubber sealing strips.
Exclusive original article [commercial authorization] reprint, excerpt and excerpt in any form are prohibited without written authorization. Focus on Hongyun rubber: learn the process formula and raw material technology of producing rubber products from recycled rubber to help you reduce costs and increase profits