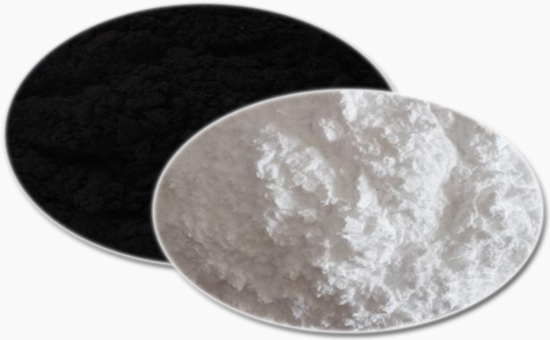
In the EPDM reinforcing and filling system, the reinforcing agent can significantly improve the tensile strength, tear resistance, abrasion resistance, etc. of the product, and the inert filler can improve the rubber processing technology, save the raw rubber and reduce the cost. When using EPDM rubber or EPDM reclaimed rubber to produce rubber products for different occasions, rubber product manufacturers need to choose appropriate reinforcing agents and fillers according to actual needs. In actual production, commonly used reinforcing fillers for EPDM rubber products fall into the following five categories.
1. Carbon black
Carbon black is a product obtained by incomplete combustion or thermal decomposition of carbon-containing substances under conditions of insufficient air. It is in the form of black powder and has a very large specific surface area. Carbon black for rubber can be divided into high wear-resistant carbon black, semi-reinforcing carbon black, fast-pressing furnace black 2YLYY514, etc. Different types of carbon black play different roles in the production of EPDM rubber products. EPDM can be filled in a large amount. Carbon black is the most commonly used reinforcing agent in the production process of its products. Choosing the right carbon black is of great significance to improving the overall performance of EPDM rubber products. .
2. White carbon black
Silica is a silicon-oxygen compound containing crystal water. The main component is silicon dioxide. It is a light-colored filler with the best reinforcing properties in rubber. It has a particle size similar to that of carbon black and has a large specific surface area. The manufacturing process can be divided into vapor phase white carbon black and precipitation white carbon black. The white carbon black has an obvious hardening effect on the rubber compound. The higher the surface activity, the more significant the increase in hardness. For every 2.5 parts of precipitation method white carbon black, the hardness of the EPDM compound increases by about 1 degree; but in actual production, white carbon is used Black-reinforced EPDM compounds can hardly reach the level of carbon black-reinforced compounds in terms of resilience, compression set, and tensile strength.
Carbon black and white carbon black are two commonly used reinforcing fillers in the production of EPDM rubber products. Compared with other types of rubber, the same kind of carbon black has the slowest hardening effect in EPDM rubber. When carbon black is used to reinforce EPDM compounds, different carbon blacks have different reinforcing properties, and EPDM products need to be considered comprehensively.When using white carbon black to reinforce light-colored EPDM products, special attention should be paid to the dispersibility of white carbon black in the rubber compound and its influence on the vulcanization performance of the rubber compound.
When using EPDM rubber or EPDM reclaimed rubber to produce rubber products, commonly used reinforcing agents include various inorganic fillers, short fibers and vulcanized rubber powder, etc. I will continue to share with you in the next issue.
Exclusive original article [commercial authorization] reprint, excerpt and excerpt in any form are prohibited without written authorization. Focus on Hongyun rubber: learn the process formula and raw material technology of producing rubber products from recycled rubber to help you reduce costs and increase profits