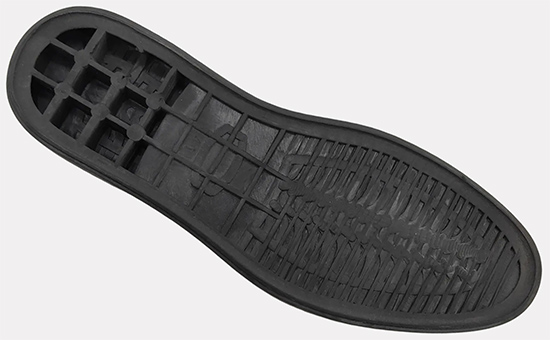
The leather sole is in direct contact with the ground and needs to withstand frequent friction, bending, etc. The rubber material is required to have excellent wear resistance, flexural resistance, elasticity and certain strength, and is generally processed with natural rubber or natural rubber/styrene-butadiene rubber. The reclaimed rubber has low price and good compatibility with natural rubber, and can be mixed into the production formula of leather soles, effectively reducing the cost of raw materials and production energy consumption under the premise of ensuring product quality.
1. The combination of natural rubber/reclaimed rubber to produce one-piece leather sole formulation
100 parts of natural rubber, 110 parts of recycled rubber, 8 parts of zinc oxide, 1.5 parts of stearic acid, 1 part of antioxidant D, 21 parts of carbon black N660, 25 parts of light calcium carbonate, 16 parts of clay, 2 parts of pine tar, 30 parts 5 parts of No. engine oil, 1.5 parts of accelerator D, 1.2 parts of accelerator DM, 2.8 parts of accelerator M, 0.3 part of accelerator TMTD, 4.4 parts of sulfur, 0.3 part of salicylic acid; total: 300 parts.
2. Combination of natural rubber/reclaimed rubber to produce molded leather sole formulation including inner and outer layer rubber
(1) The formula of natural rubber molded leather sole outer layer mixed with reclaimed rubber: 75 parts of natural rubber, 25 parts of styrene-butadiene rubber, 80 parts of reclaimed rubber, 5 parts of zinc oxide, 2.5 parts of stearic acid, 0.5 parts of antioxidant A, Anti-aging agent D 0.5 parts, paraffin wax 0.5 parts, carbon black N330 40 parts, light calcium carbonate 30 parts, asphalt 3.5 parts, coumarone resin 10 parts, accelerator D 1.2 parts, accelerator DM 1.4 parts, accelerator M 1.3 parts, sulfur 3.4 parts, salicylic acid 0.2 parts, total: 280 parts.
(2) The formula of natural rubber molded leather sole with reclaimed rubber: 70 parts of natural rubber, 30 parts of styrene-butadiene rubber, 160 parts of reclaimed rubber, 8 parts of zinc oxide, 2.6 parts of stearic acid, 1 part of antioxidant A, 1 part of antioxidant D, 32 parts of carbon black N330, 31 parts of light calcium carbonate, 3 parts of asphalt, 7 parts of coumarone resin, 1.3 parts of accelerator D, 1.5 parts of accelerator DM, 2 parts of accelerator M, accelerator 0.4 parts of TMTD, 5.6 parts of sulfur, 0.6 parts of salicylic acid; total: 357 parts.
The leather sole made of natural rubber as the main raw material has the problems of wear resistance, slip resistance, good elasticity, high softness, good elongation, stable shrinkage, bending resistance, and not easy to break; but there is the problem of easy frosting. As a replacement raw material for high-priced natural rubber, the amount of sulfur and accelerators can be increased by about 20% compared with natural rubber. Not as prone to blooming problems as pure natural rubber.
When using reclaimed rubber to reduce the production cost of natural rubber leather soles, latex reclaimed rubber, tire reclaimed rubber and rubber shoe reclaimed rubber in the reclaimed rubber can all be used. Will continue to share relevant questions with you.
Exclusive original article [commercial authorization] reprint, excerpt and excerpt in any form are prohibited without written authorization. Focus on Hongyun rubber: learn the process formula and raw material technology of producing rubber products from recycled rubber to help you reduce costs and increase profits