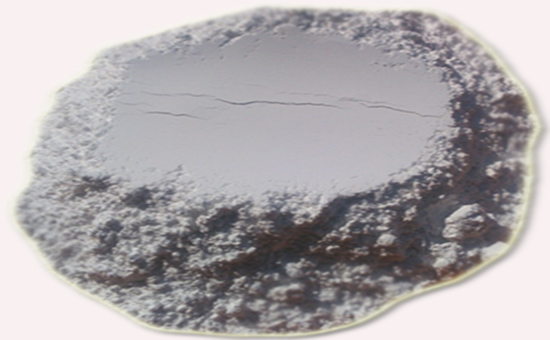
Calcium silicate is a white inorganic powder consisting of 45%-47% silica, 44%-46% calcium oxide, water and a very small amount of iron oxide. Under reasonable formula, calcium silicate is supplemented in latex reclaimed rubber. The strong effect is obviously superior to natural rubber, and it is better than the carbon black to reinforce the latex reclaimed rubber. It is often used together with carbon black to significantly improve the vulcanization properties and physical and mechanical properties of the latex product. How does calcium silicate affect NR reclaimed rubber? Vulcanization properties? What mechanical indicators can be improved?
1. Effect of calcium silicate on vulcanization properties of latex reclaimed rubber
The surface of calcium silicate contains a small amount of acidic carboxyl groups, the ratio of calcium silicate/carbon black increases, and the scorch time of latex reclaimed rubber compound decreases, which will reduce the safety of scorch to a certain extent; from another angle It can be seen that the alkaline filler can improve the crosslinking and vulcanization efficiency. With the increase of the amount of weakly alkaline calcium silicate, the vulcanization efficiency of the latex reclaimed rubber is improved; the calcium silicate micropowder has similar carbon black in the microstructure, and the void structure Rich, large specific surface area, high surface activity, latex reclaimed rubber itself has low molecular weight, so calcium silicate can be chemically combined with NR reclaimed rubber to promote cross-linking and increase vulcanization efficiency.
2. Effect of calcium silicate on physical properties of latex reclaimed rubber
Studies have shown that the ratio of calcium silicate/carbon black increases, the density of latex reclaimed rubber increases slightly, the internal molecular chain is softer, the hardness is slightly reduced, and the fluidity of latex reclaimed rubber is improved; the tensile strength and elongation at break of latex reclaimed rubber It will increase greatly with the increasing proportion of calcium silicate/carbon black. Generally, the tensile strength and elongation at break of NR reclaimed rubber reinforced with calcium silicate are three times that of carbon black.
The latex reclaimed rubber itself has low molecular weight, low molecular chain softness, and calcium silicate can be uniformly dispersed in the rubber compound. The latex reclaimed rubber can enter the honeycomb microporous structure of calcium silicate under the action of shearing and extrusion, improving The interfacial force between the rubber compound and the filler, the calcium silicate and the latex reclaimed rubber can be firmly combined to improve the physical and mechanical properties of the NR reclaimed rubber.
At present, the most commonly used reinforcing filler in the rubber products industry is carbon black. In the light-colored rubber products, high-priced white carbon black or nano-scale inorganic particles are often used; when using latex reclaimed rubber to produce light-colored rubber products, if these high-priced shallow products are used, Color-reinforced fillers will undoubtedly bring greater cost pressure to rubber products companies. Are you considering using calcium silicate? Xiaobian said: When using latex reclaimed rubber instead of natural rubber to produce rubber products, not only the rubber cost, but also the cost of various compounding agents should be calculated, and the quality of latex reclaimed rubber products should be reduced as much as possible. Production costs.
Exclusive original article [commercial authorization] reprint, excerpt and excerpt in any form are prohibited without written authorization. Focus on Hongyun rubber: learn the process formula and raw material technology of producing rubber products from recycled rubber to help you reduce costs and increase profits