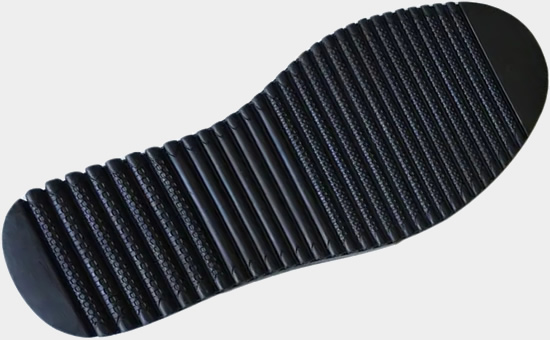
Moulded rubber outsole is generally made of natural rubber, styrene butadiene rubber and cis polybutadiene rubber. In order to further reduce production costs, rubber sole manufacturers try to add recycled rubber or recycled rubber powder to the formula; Properly adjusting the formula can reduce the raw material cost and production energy consumption on the premise of ensuring the service performance and life of the molded outsole. Xiao Bian will share with you today the reference formula of rubber molding outsole mixed with tire powder and the coordination and adjustment skills.
1. Practical formula of natural rubber+cis-1,4-polybutadiene rubber+tire rubber powder for producing molded outsole
60 portions of natural rubber, 40 portions of cis polybutadiene rubber, 100 portions of tire powder, 5 portions of zinc oxide, 0.6 portions of stearic acid, 1 portion of antioxidant SP, 45 portions of white carbon black, 6 portions of naphthenic oil, 6 portions of coumarone resin, 2.2 portions of silane coupling agent, 2 portions of white carbon black activator, 0.3 portions of accelerator D, 1.5 portions of accelerator DM, 0.3 portions of accelerator TMTD, and 2.1 portions of sulfur; Total: 272 copies.
2. Practical formula for production of molded outsole with natural rubber+styrene butadiene rubber+recycled rubber+tire rubber powder
40 shares of natural rubber, 60 shares of styrene butadiene rubber, 25 shares of recycled rubber, 20 shares of tire rubber powder, 5 shares of zinc oxide, 3.1 shares of stearic acid, 60 shares of carbon black N330, 10 shares of engine oil, 18 shares of coumarone resin, 30 shares of clay, 5 shares of industrial grease, 0.8 shares of accelerator M, 0.7 shares of accelerator D, 1 share of accelerator CZ, 2.2 shares of sulfur, 0.2 shares of salicylic acid; Total: 281 copies.
3. Key points of formula optimization for reducing cost by using tire powder in molded rubber outsole
The cost of rubber sole formula with natural rubber, styrene butadiene rubber or cis-1,4-polybutadiene rubber as main raw materials is reduced by mixing tire powder. It is recommended to use tire powder 2SLYY14 among 60-80 meshes, which is not expensive and has better mixing effect. If you want to further reduce the production cost of the molded outsole, you can use an appropriate amount of recycled tire rubber and recycled rubber for rubber shoes in the molded outsole formula containing tire rubber powder.
The tensile strength, elongation at break and tear strength of vulcanizate decreased with the increase of the amount of rubber powder when the same rubber compound was mixed with tire powder; When the amount of vulcanized rubber powder exceeds a certain value, the indicators of the sports sole will obviously decline, so it is necessary to reasonably control the amount of tire rubber powder. In actual production, the performance requirements of rubber molded outsole with different index requirements are different, and the mixing amount of tire rubber powder varies greatly. Later, Xiaobian will continue to share with you the key points of the production process of molded rubber outsole mixed with tire rubber powder.
Exclusive original article [commercial authorization] reprint, excerpt and excerpt in any form are prohibited without written authorization. Focus on Hongyun rubber: learn the process formula and raw material technology of producing rubber products from recycled rubber to help you reduce costs and increase profits