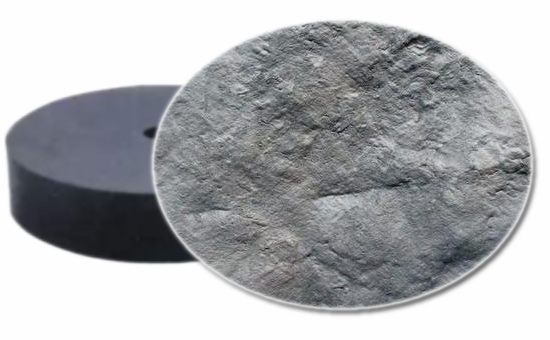
Scorch is an early vulcanization phenomenon that occurs during rubber processing or during parking before vulcanization, that is, self-sulfur, a problem often encountered in the production of rubber products. The use of anti-scorching agents can effectively avoid scorching of rubber compounds. When reclaimed rubber is used to produce rubber products, vulcanizing agents, accelerators, reinforcing agents, fillers, and even anti-aging agents will affect the safety of rubber scorch. Different kinds of compounding agents have different effects on the safety of regenerated rubber scorch The rubber product manufacturer needs to adjust the type and dosage of the compounding agent in the formula reasonably.
1. The compounding agent of the vulcanization system affects the safety of regenerated rubber scorch
When using reclaimed rubber to produce rubber products, excessive amounts of vulcanizing agent and accelerator in the formulation and unreasonable coordination of the vulcanizing system are the main reasons for the scorching of the rubber compound. The type and amount of accelerator have a great influence on the safety of regenerated rubber scorch Large, different varieties of accelerators have different effects on the safety of rubber processing. Rubber product manufacturers need to choose the appropriate anti-scorching agent according to the type of rubber accelerator. Agent HTM can effectively avoid the problem of scorch of reclaimed rubber.
2. Reinforcing system compounding agent affects the safety of regenerated rubber scorch
Carbon black and white carbon black are commonly used reinforcing agents in the production of reclaimed rubber products. Because fine particle carbon black and white carbon black are difficult to disperse during the mixing of reclaimed rubber and generate heat quickly, it will significantly increase the occurrence of scorching of rubber Probability, the greater the amount, the shorter the scorch time. For carbon black products, high-structure carbon black will shorten the scorch time of reclaimed rubber, acid carbon black with high oxygen content and low ph value has a longer scorch time like channel black; the structure of carbon black can be seen , Surface acidity and alkalinity and oxygen content will affect the scorch safety of reclaimed rubber products.
Therefore, when recycled rubber products manufacturers use carbon black or white carbon black 2LLYY429 for reinforcement, they must choose the appropriate variety of carbon black and white carbon black to control the amount of reinforcing agent. Tendency to reduce certain raw material costs.
3. Anti-aging system compounding agent affects the safety of regenerated rubber scorch
Reasonable anti-aging system design is of great significance to improve the aging resistance of recycled rubber products and prolong the service life of products. However, in actual production, different types of antioxidants have different effects on scorch, and some antioxidants can prevent scorch. Under normal circumstances, ketoamine antioxidants, quinoline antioxidants, such as common antioxidant RD, antioxidant AW can promote scorch; phenylenediamine antioxidants have a certain role in promoting scorch, different varieties The scorch-promoting effect of the p-phenylenediamine anti-aging agent is different. The common ones are anti-aging agent TMDQ, anti-aging agent DPA, anti-aging agent DNPD and anti-aging agent DAPD.
It is worth mentioning that the anti-aging agent 264 and anti-aging agent 2246 can play a certain anti-scorching role in the production of recycled rubber products, while the general-purpose anti-aging agent D has almost no effect on the scorch performance of recycled rubber, it is recommended to use.
When using reclaimed rubber to produce rubber products, softeners and fillers have little effect on the scorch performance of rubber compounds. Rubber product manufacturers must choose a suitable variety of compounding agents. In addition to the use of anti-scorching agents, the amount of stearic acid and other acidic substances can be appropriately increased to reduce the scorch speed without affecting the vulcanization speed. Improving the safety of rubber scorch and avoiding scorch can significantly improve the quality and yield of recycled rubber products, reduce raw material costs, and avoid unnecessary economic losses.
Exclusive original article [commercial authorization] reprint, excerpt and excerpt in any form are prohibited without written authorization. Focus on Hongyun rubber: learn the process formula and raw material technology of producing rubber products from recycled rubber to help you reduce costs and increase profits