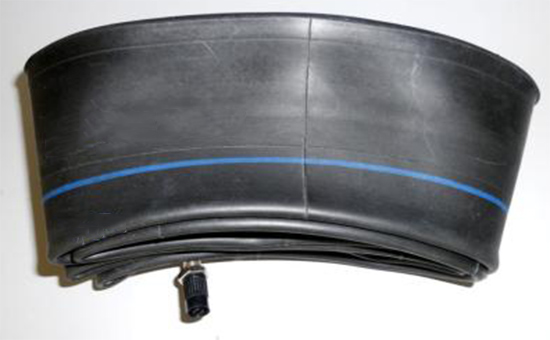
In the production process, the thickness of the inner tube of the butyl inner tube is uneven, and the joint crack is the most common two problems. However, in actual production, the same reason may cause other problems in the inner tube, such as when the joint is stuck with talc. When powder or release agent, not only will the joint be weakly lapped, but also a white line will be formed after vulcanization, and the joint will be cracked; in addition, when the joint contains talcum powder, the butyl rubber will cover the talcum powder when flowing. Causes the inner tube to appear heavy skin.
1. The butyl inner tube joint is too thin
The butyl inner tube joint not only has cracks and heavy skin, but also may be thin at the joint. There are two main reasons for this problem. One is that the joint pressure is insufficient, and the other is that the glue has insufficient parking time. Therefore, it is necessary to properly control the joint pressure and the compounding time during the production of the butyl inner tube.
2. Causes and solutions for the occurrence of defects in the butyl inner tube valve
During the production of butyl rubber inner tube, cracks, heavy skin or air bubbles at the edge of the valve and air bubbles between the rubber pad and the tire body may occur. When cracks or heavy skins appear on the edge of the valve pad, the manufacturer needs to check whether there is a problem of poor adhesion between the valve pad and the tire. If not, you need to consider whether the edge of the pad is too thick or surface. Containing talcum powder.
Once the butyl rubber or compounding agent is wetted during the parking process, or the moisture content of the compound and the compounding agent is too high, or the volatile component is reacted between the compounding agent and the compounding agent, the butyl rubber is produced during vulcanization. Bubbles, so that the edge of the butyl inner tube valve, the rubber pad and the inner tube of the inner tube will gather bubbles; the amount of vulcanizing agent, accelerator is insufficient or partially agglomerated during the production process, and the vulcanization temperature and vulcanization pressure are not up to standard. The rubber is low in sulfur. If it is just this part, it will create bubbles at the edge of the valve and between the rubber pad and the tire casing. In addition, when the butyl inner tube is in the upper valve, it must be ensured that the glue is dry, and the glue will not be dry and will also generate bubbles.
3. The surface of the butyl inner tube is not flat
Improper process operation in the production process of butyl inner tube can easily lead to problems such as pleats, alum, lack of glue and pockmark on the surface of the carcass. Among them, various types of dead pleats and live pleats are mainly caused by improper size or over-formation of semi-finished products. When the butyl inner tube is vulcanized, the steam will break into the cavity, and the rubber will not contact the model because of the gas between the model and the inner tube. The inner surface of the inner tube has alum or pockmark due to lack of glue; the internal pressure is insufficient and the vulcanization process The size of the vulcanization pressure fluctuated, and the butyl inner carcass appeared to be defective.
What problems will be encountered in the production of butyl inner tube? Xiaobian and you continue to "explore".
Exclusive original article [commercial authorization] reprint, excerpt and excerpt in any form are prohibited without written authorization. Focus on Hongyun rubber: learn the process formula and raw material technology of producing rubber products from recycled rubber to help you reduce costs and increase profits