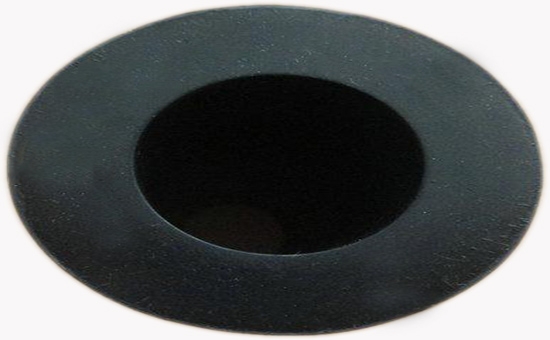
Nitrile rubber has excellent oil resistance, cold resistance, abrasion resistance and chemical stability. It can be used to produce oil, abrasion and heat resistant rubber products and can maintain good performance for a long time. In the production process of rubber products, mixing is the most important production process. It is a process in which the compounding agent is uniformly dispersed in the raw rubber, which directly affects the quality of the finished product. When nitrile rubber is used to produce rubber products, due to the limitation of nitrile's own process performance, problems such as sticking, roll off, and poor dispersion are prone to occur during mixing. How to solve it?
1. Sticky roller
Nitrile rubber is very polar, and it is easy to stick to the roller when the roller temperature is high or the amount of plasticizer is large. The center of solving the problem of sticking to the roller during nitrile mixing is to remove the adhesion. Choosing rubber with high Mooney viscosity, using fast pressing black or medium super wear-resistant carbon black, using migratory plasticizer, appropriately increasing the amount of lubricant, avoiding the use of magnesium oxide and active light calcium, etc., can reduce the nitrile viscosity. Roll probability. From the perspective of process operation, appropriately reducing the temperature of the roller and increasing the roller distance can also avoid sticking to the roller during the mixing of nitrile rubber.
2. Roll off
Nitrile rubber itself has poor adhesion, so it is easy to roll off during roller processing. Increasing the adhesiveness of the compound is the key to avoiding roll off of nitrile rubber. From the point of view of operating technology, appropriately reducing the roll distance and increasing the temperature of the roll can increase the adhesion of nitrile rubber. From the formulation point of view, increasing the amount of filler (about 50 parts of high wear-resistant carbon black), using rosin or phenolic resin as a tackifier, increasing the amount of plasticizer to more than 10 parts, and using a moderate amount of liquid nitrile can all increase the amount of glue. Adhesion of materials to avoid roll-off during butyronitrile mixing.
3. Poor dispersion of low hardness formula
When nitrile rubber is used to produce low-hardness rubber products, poor dispersion is likely to occur during mixing. The use of high Mooney nitrile rubber, the appropriate amount of dioctyl phthalate, and the use of ointment to replace part of the plasticizer 2YLYY628 can improve the poor mixing and dispersion of low-hardness formulations. From the point of view of process operation, different types of plasticizers are recommended to be added separately. When the internal mixer is mixed at high temperature, it is recommended to add more than 80% of the material. After cooling, two-stage mixing is carried out to significantly improve the compounding agent in the low-hardness compound. Degree of uniform dispersion.
4. The high hardness formula generates too much heat
High hardness nitrile rubber products generate a lot of heat during the mixing process. It is recommended to choose low Mooney nitrile rubber, combined with high styrene resin and phenolic resin to reduce the viscosity of the rubber compound. From the perspective of the operating conditions of the production process, it is recommended to add fillers separately and combine materials with different particle sizes; reduce the feeding amount of the internal mixer; cool the roller to avoid scorching; thereby improve the heat generation during the mixing of high hardness nitrile rubber products High question.
Mixing is the process of mixing raw rubber or plasticized rubber and compounding agents into a rubber compound by a rubber mixing machine. After mixing, the granular compounding agent is in the dispersed phase and the raw rubber is in the continuous phase. When nitrile rubber is used to produce rubber products, the rubber material can be fully and uniformly mixed to provide better conditions for subsequent production process operations. In actual production, the use of reclaimed rubber in the formula of pure nitrile rubber products can also improve the mixing process performance of the rubber to a certain extent and reduce the heat generation and mixing power consumption. The editor will continue to discuss with you later.
Exclusive original article [commercial authorization] reprint, excerpt and excerpt in any form are prohibited without written authorization. Focus on Hongyun rubber: learn the process formula and raw material technology of producing rubber products from recycled rubber to help you reduce costs and increase profits