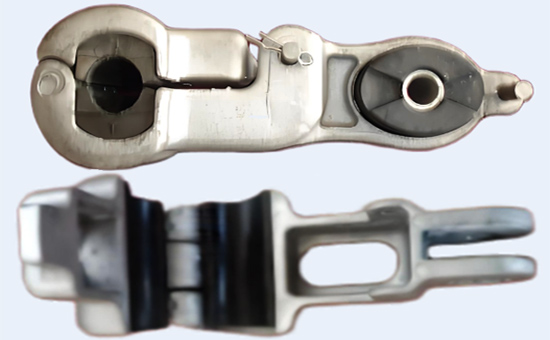
High temperature resistant damping spacer rubber parts are a kind of rubber parts applied to power transmission line spacers, mainly used to prevent whipping among wires, inhibit breeze vibration and secondary distance oscillation, generally made of EPDM rubber, chlorinated polyethylene, etc. as the main raw materials. EPDM recycled rubber retains the basic performance characteristics of EPDM and can be mixed into EPDM or EPDM/chlorinated polyethylene blend materials to reduce the production cost of high-temperature damping spacer rubber parts.
1. Performance requirements of high-temperature damping spacer rubber parts
High temperature resistant damping spacer rubber parts are widely used in high-voltage and ultra-high voltage transmission lines, long-term outdoor work, and the rubber materials used need to have good high and low temperature resistance, weather resistance, and ozone resistance. It has high tensile strength, wear resistance and damping, low compression set, and meets the tensile force requirements of spacer rods during installation and use. The high tear elongation can ensure that the rubber parts have a certain deformation ability when subjected to force and are not easy to break, ensuring a stable grip on the wire.
2. Mixing skills of EPDM recycled rubber in high-temperature damping spacer rubber parts
(1) Advantages
EPDM recycled rubber retains the structural characteristics of EPDM rubber main chain saturation and side chain small amount of unsaturation, and has good high and low temperature resistance, weather resistance and ozone resistance, which can meet the basic environmental adaptation needs of spacer rubber parts. The price of EPDM recycled rubber is much lower than that of the original rubber, and the production of high-temperature resistant damping spacer rubber parts E5LYY34 in an appropriate proportion with EPDM rubber can effectively reduce the cost of raw materials. EPDM recycled rubber has good fluidity and plasticity, which can improve the processing process of rubber and reduce the power consumption in the process of compounding and vulcanization.
(2) Mixing skills
When the performance requirements of high-temperature damping spacer rubber parts are high, EPDM can be used in conjunction with EPDM recycled rubber to produce rubber parts, and the amount of EPDM recycled rubber is at controlled about 10%-20%. When using EPDM recycled rubber to reduce costs for high-temperature damping spacer rubber parts with moderate performance requirements, EPDM recycled rubber and EPDM / chlorinated polyethylene can be used to blend the system, and the amount of recycled rubber can be increased to 20%-30%.
When the high-temperature damping spacer rubber parts are mixed with EPDM recycled rubber, it is recommended to preheat and soften the EPDM recycled rubber first, and then fully mix it with EPDM in the opening machine or mixer, and the mixing time is appropriately extended by 1-2 minutes to ensure that the recycled rubber and EPDM rubber form a stable blending structure.
3. EPDM/EPDM recycled rubber is used to produce high-temperature damping spacer rubber parts formula design points
(1) Vulcanization system design
When producing high-temperature resistant damping spacer rubber parts with EPDM/recycled rubber, a low-sulfur and high-vulcanization system or a sulfur-free vulcanization system can be used to improve the heat resistance of the compound, and if necessary, a combination of peroxide and sulfur can be used, and peroxide can be used as the main vulcanizing agent, sulfur assists cross-linking, and improves the heat resistance and dynamic mechanical properties of spacer rubber parts. The accelerators CZ and TMTD were used together with vulcanizing agents to optimize the vulcanization rate and scorching safety.
(2) Reinforcement filling system design
EPDM/EPDM recycled rubber is reinforced with high wear-resistant carbon black, which can give vulcanized rubber good mechanical properties, such as carbon black N330; Used with semi-reinforced carbon black to reduce heat generation, improve damping performance, vulcanized adhesives obtain better high-temperature aging resistance and low compression set properties, such as carbon black N774.
(3) Softening system design
The use of paraffin oil, naphthenic oil, etc. as softeners, has good compatibility with EPDM compounds, can improve the fluidity of EPDM rubber/EPDM recycled adhesive, and is not easy to volatilize at high temperatures. Avoid using aromatic oils, poor weather resistance.
The reasonable use of EPDM recycled rubber in high-temperature damping spacer rubber parts can balance performance and cost, and reasonably design the rubber formula, which can not only retain the good high and low temperature resistance and weather resistance of EPDM rubber materials, but also meet the use needs of spacer rubber and reduce raw material costs and production energy consumption. In actual production, high-temperature resistant damping spacer rubber parts mixed with EPDM recycled rubber still need to be appropriately adjusted to the production process parameters, especially the temperature and time of mixing and vulcanization, and discuss related issues with you later.
Exclusive original article [commercial authorization] reprint, excerpt and excerpt in any form are prohibited without written authorization. Focus on Hongyun rubber: learn the process formula and raw material technology of producing rubber products from recycled rubber to help you reduce costs and increase profits