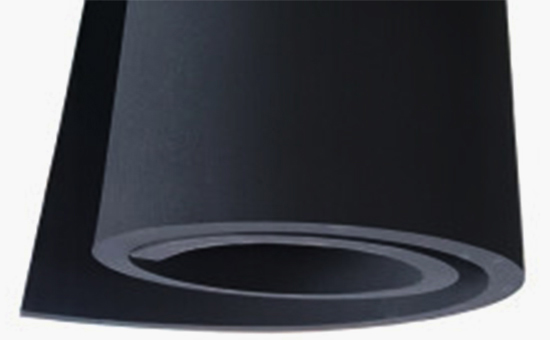
EPDM reclaimed rubber is resistant to high and low temperatures, aging, and high insulation. It can be used alone or in combination with EPDM rubber, butyl rubber, etc. to produce foam rubber products such as heat-resistant foam rubber plate, sponge sealing strip, etc. When using EPDM recycled rubber to produce foam rubber products, selecting appropriate foaming agents and designing a reasonable foaming system are the basis for ensuring the performance and service life of EPDM recycled rubber foam products.
1. Common foaming agents for EPDM recycled rubber sponge foam rubber products
Rubber foaming agents can be divided into organic foaming agents and inorganic foaming agents. When using EPDM recycled rubber to produce sponge rubber, suitable foaming agent products need to be selected based on actual needs and the performance characteristics of the foaming agent.
(1) Inorganic foaming agents: Inorganic foaming agents are mainly carbonates, among which sodium bicarbonate has good safety and is widely used in EPDM regenerated rubber foam rubber. Sodium bicarbonate is used as a foaming agent, with a general dosage of 5-15 parts and a certain amount of stearic acid to promote its decomposition. The resulting sponge has a small and uniform pore size; However, due to the small gas generation of sodium bicarbonate, it is usually recommended to use it in combination with organic foaming agents.
(2) Organic foaming agents: Common types of organic foaming agents include foaming agent AC, foaming agent H, foaming agent OBSH, urea, etc.
Foaming agent AC has a large gas generation capacity and low gas permeability, resulting in products with good skinning and odorless characteristics, and is widely used in EPDM sponge sealing strips. The foaming agent OBSH has the characteristics of low decomposition temperature, fast decomposition speed, no coloring pollution, and odorless and non-toxic decomposition products. It has easy pore formation, uniform and delicate foam structure, and good dimensional stability of the sponge. It is widely used in EPDM models or extruded sponge products; The foaming agent OBSH has a small gas generation capacity and is difficult to obtain high-density sponges with high porosity, so it is usually used in conjunction with foaming agent AC.
2. Design basis for foam system of EPDM recycled rubber sponge foam rubber products
When producing sponge foam rubber products using EPDM recycled rubber as the main raw material, the matching of vulcanization speed and foaming speed is very important. A foaming agent with appropriate decomposition temperature should be selected based on the molding process, and attention should be paid to the application of foaming agent 2SLYY412, so that the decomposition of the foaming agent can be carried out within the controllable temperature range of vulcanization. However, the decomposition rate of foaming agents is greatly influenced by the additives in the rubber compound, making it more difficult to adjust than the vulcanization rate. Therefore, it is usually through the adjustment of the vulcanization system to adapt to the corresponding foaming agent system after the foaming agent system is determined.
In actual production, when vulcanization is faster than foaming, the viscosity of the rubber material increases, which will cause difficulty in foaming; When foaming is faster than vulcanization, gas is easy to escape, resulting in a decrease in foaming efficiency, insufficient foaming, and an unsmooth crust surface. When using EPDM recycled rubber to reduce sponge foam rubber products, it is not only necessary to design the foam system reasonably, but also to choose a suitable vulcanization system to cooperate. The editor will continue to discuss relevant issues with you in the future.
Exclusive original article [commercial authorization] reprint, excerpt and excerpt in any form are prohibited without written authorization. Focus on Hongyun rubber: learn the process formula and raw material technology of producing rubber products from recycled rubber to help you reduce costs and increase profits