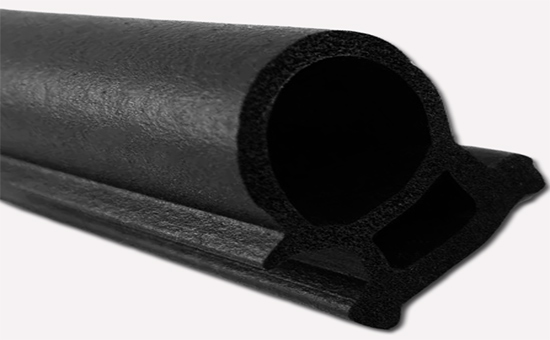
EPDM reclaimed rubber has the characteristics of high and low temperature resistance, ozone resistance and weather resistance, and can be used alone or in combination with EPDM rubber to produce rubber products. When using EPDM reclaimed rubber or ethylene-propylene rubber/reclaimed rubber to produce rubber products, full mixing is the basis for the smooth progress of the subsequent process. Therefore, it is necessary to fully understand the mixing characteristics of various raw materials. Xiaobian will share with you today. Share the mixing characteristics of commonly used raw and auxiliary materials for EPDM reclaimed rubber products.
1. Mixing characteristics of ethylene-propylene rubber and EPDM reclaimed rubber
Ethylene-propylene rubber is a typical non-polar rubber with low degree of unsaturation, poor wettability to powdery fillers and compounding agents, and slow mixing speed during mixing. performance. Compared with the original ethylene-propylene rubber, the EPDM reclaimed rubber 2ELYY524 has good plasticity, the compounding agent is evenly dispersed, and the power consumption of the rubber compound is much less than that of the original rubber. When EPDM rubber/reclaimed rubber is combined to produce rubber products, the addition of reclaimed rubber can improve the mixing performance of the original rubber to a certain extent.
When mixing EPDM original rubber/EPDM reclaimed rubber, the mixing temperature should be appropriately increased in order to ensure the fast and uniform dispersion of the filler.
2. Mixing characteristics of sulfur in EPDM reclaimed rubber products
Sulfur is one of the commonly used vulcanizing agents for EPDM reclaimed rubber products. It has a low melting point. When the temperature is higher than 100 °C, liquefaction and agglomeration will occur, and it is difficult to uniformly disperse in the rubber compound. Therefore, when EPDM reclaimed rubber is mixed with sulfur, the temperature of the rubber must be cooled to below 100 °C. In actual production, sulfur is generally added in the final stage of mixing to avoid the scorch problem of ethylene-propylene rubber/reclaimed rubber.
3. The mixing characteristics of zinc oxide in EPDM reclaimed rubber products
Zinc oxide is generally used as an active agent in EPDM reclaimed rubber products, which can significantly increase the vulcanization speed; or as a filler. During the mixing process, since zinc oxide has the same negative charge as the raw rubber, the same sex repels each other, so although zinc oxide is easily mixed into the EPDM reclaimed rubber, it is very difficult to disperse. In actual production, manufacturers of EPDM reclaimed rubber products can use pre-granulated zinc oxide granules, or choose zinc oxide products with finer particles to improve the dispersibility of zinc oxide in EPDM reclaimed rubber products.
In the production of EPDM reclaimed rubber products, the dosage of reinforcing agents and fillers is very large; softeners are also important additives to improve EPDM rubber compounds, and their dispersibility in the rubber compounds has an impact on the quality of reclaimed rubber compounds. The impact is great. Tomorrow, the editor will continue to discuss with you the mixing characteristics of reinforcing agents, fillers, softeners, plasticizers and other compounds commonly used in EPDM reclaimed rubber products.
Exclusive original article [commercial authorization] reprint, excerpt and excerpt in any form are prohibited without written authorization. Focus on Hongyun rubber: learn the process formula and raw material technology of producing rubber products from recycled rubber to help you reduce costs and increase profits