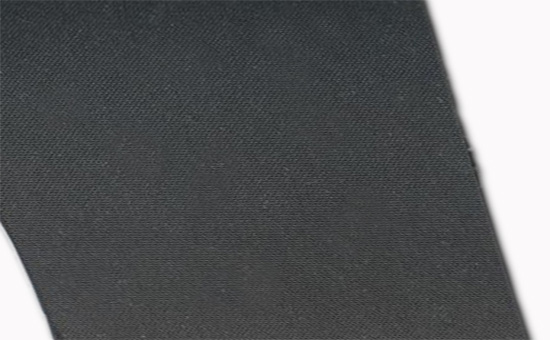
The rubber lining can reduce the impact and corrosion of the pipeline conveying medium on the external structure through its own performance characteristics, so the shock absorption and chemical stability of the rubber used are relatively high. Both EPDM rubber and waste EPDM rubber products processed into EPDM reclaimed rubber have excellent ozone resistance and weathering resistance, and can be used to produce rubber linings. So what applications can the rubber lining produced with EPDM as the main raw material be used? How should rubber products manufacturers design formulas?
1. Performance characteristics of EPDM rubber lining
EPDM rubber and EPDM reclaimed rubber can impart good heat resistance and chemical stability to the rubber lining. Generally, it has good resistance to strong polar solvents such as alcohols, ketones and esters, as well as inorganic salts, hydrochloric acid and strong alkali solutions. High tolerance; it can maintain good performance in phosphoric acid or ethylene glycol at 100°C. It should be noted that the EPDM compound is not resistant to concentrated sulfuric acid and concentrated nitric acid, and can only be used at room temperature for acetic acid and glacial acetic acid.
In addition, the resistance of EPDM rubber to animal and vegetable oils is slightly better than that of natural rubber and styrene butadiene rubber, but it is completely inapplicable to mineral oil.
2. Application method of EPDM/reclaimed rubber
When using EPDM rubber or EPDM reclaimed rubber to produce rubber linings, you can choose to use EPDM virgin rubber alone or completely use EPDM reclaimed rubber to effectively reduce the cost of raw materials. The combined use of propylene rubber and reclaimed rubber 2YLYY122; the combined use of EPDM/reclaimed rubber can better coordinate the relationship among product physical properties and production costs. In actual production, an appropriate amount of butyl rubber or butyl reclaimed rubber can be added to the EPDM lining formula to further improve the air tightness of the rubber and delay aging.
3. EPDM rubber lining formula
100 parts of EPDM rubber, 70 parts of furnace carbon black, 5 parts of process oil, 1 part of antioxidant, 5 parts of zinc oxide, 1.5 parts of sulfur, 1.5 parts of accelerator TS, 0.5 parts of accelerator M; total: 184.5 parts . In the above formula, part of the EPDM virgin rubber can be replaced with EPDM reclaimed rubber, or the EPDM reclaimed rubber can be used to completely replace the EPDM virgin rubber. Adjust the formula, including increasing the amount of vulcanizing agent, accelerator, and strengthening agent in an appropriate amount, and appropriately adjusting the variety and amount of antioxidant and operating oil, so as to further optimize product quality while reducing costs.
4. Selection of EPDM reclaimed rubber for rubber lining
The rubber lining requires no bubbles, pinholes, or impurities appear inside the rubber, it is not easy to crack during use, and it has good adhesion with other materials. When using EPDM reclaimed rubber to reduce the production cost of rubber linings, it is recommended to choose reclaimed rubber that is close to the indicators of the lining and slightly lower in hardness. Choose products with high fineness and no impurities to further improve the rubber lining while reducing costs. Finished product index.
Both EPDM rubber and EPDM reclaimed rubber are ideal raw materials for the production of rubber linings. Product manufacturers can select appropriate raw materials according to actual needs, rationally design rubber product formulas, and produce more cost-effective products to effectively improve economic benefits.
Exclusive original article [commercial authorization] reprint, excerpt and excerpt in any form are prohibited without written authorization. Focus on Hongyun rubber: learn the process formula and raw material technology of producing rubber products from recycled rubber to help you reduce costs and increase profits