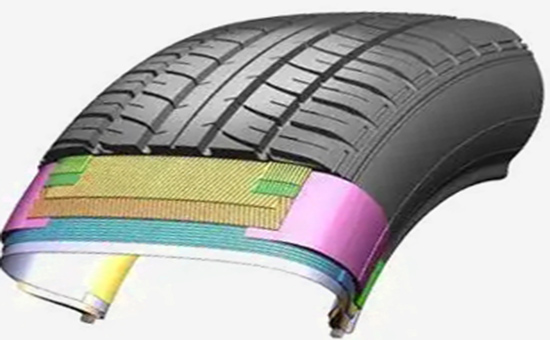
The triangular rubber core of the automobile tire bead is an important part of the tire bead, which provides the necessary shape and volume for the bead, so that the bead can maintain a stable shape, disperse and cushion the impact force of the bead part and the interaction force among the tire and the rim. The bead triangle rubber core is generally processed with natural rubber as the main raw material, and a large amount of reclaimed rubber is mixed with a reasonable design of the triangle rubber core formula, which can effectively reduce the cost of raw materials under the premise of ensuring the performance of the finished rubber material.
1. Completely use natural rubber to produce tire bead triangle rubber core single core vulcanization formula
100 parts of natural rubber, 4 parts of zinc oxide, 3.5 parts of stearic acid, 1.5 parts of antioxidant 4010, 1 part of antioxidant D, 60 parts of carbon black N330, 20 parts of mixed carbon black, 3 parts of pine tar, 0.6 parts of accelerator NOBS, 2.8 parts of sulfur; Total 196.4 copies.
2. Natural rubber/reclaimed rubber is used to produce a single core rubber vulcanization formula for the triangular rubber core of automobile tire beads
50 parts of natural rubber, 50 parts of recycled rubber, 2.5 parts of zinc oxide, 1.5 parts of stearic acid, 1 part of antioxidant D, 40 parts of carbon black N774, 10 parts of recycled carbon black, 30 parts of clay, 55 parts of light calcium carbonate, 5 parts of pine tar, 2.5 parts of asphalt, 0.25 parts of accelerator M, 0.6 parts of accelerator DM, 0.05 parts of accelerator TMTD, 2.6 parts of sulfur; A total of 251 copies.
30 parts of natural rubber, 70 parts of recycled rubber, 2.5 parts of zinc oxide, 0.9 parts of stearic acid, 1 part of antioxidant RD, 30 parts of carbon black N774, 100 parts of light calcium carbonate, 2.5 parts of pine tar, 1.5 parts of asphalt, 0.45 parts of accelerator M, 1.75 parts of sulfur; Total 240.6 copies.
3. Natural rubber/reclaimed rubber production of automobile tire bead triangle rubber core single core rubber formula design points
When natural rubber/reclaimed rubber is used together to produce the triangular rubber core of the tire bead, the rubber material is required to have high hardness and good flexural resistance and anti-aging performance, and the ordinary sulfur-accelerator system is generally used, and the high wear-resistant carbon black and semi-reinforced carbon black reinforcing E4LYY1231 are used, and the mechanical strength of vulcanized rubber is higher; When using softeners to improve the performance of rubber processing technology, the amount of oil softener should be reduced as much as possible, and the combination of high carbon black and low oil content can give vulcanized rubber a high hardness.
If you want to further improve the hardness of the rubber compound, you can use an appropriate amount of hardening agent, reduce the amount of carbon black, and improve the operation performance of the rubber mixing and extrusion process. The appropriate amount of surface tackifier is used to improve the adhesion of natural rubber/reclaimed rubber semi-finished products, which is helpful for molding operations and improves the quality of tire blanks. When natural rubber/reclaimed rubber is used to produce the triangle rubber core of automobile tire beads, it can also be used with an appropriate amount of styrene-butadiene rubber and butadiene rubber.
Exclusive original article [commercial authorization] reprint, excerpt and excerpt in any form are prohibited without written authorization. Focus on Hongyun rubber: learn the process formula and raw material technology of producing rubber products from recycled rubber to help you reduce costs and increase profits