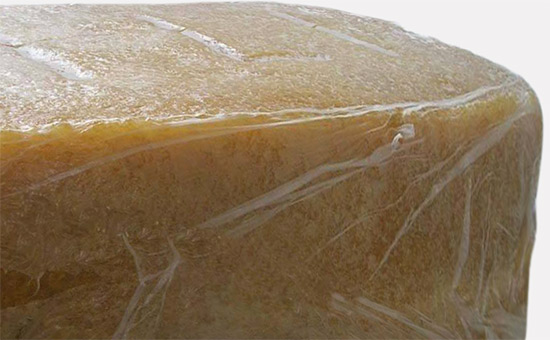
Natural rubber is the most widely used general rubber in the rubber products industry. Its main component is rubber hydrocarbon, which has good elasticity, high mechanical strength, small lag loss, low heat generation due to repeated deformation, and low heat generation. It is widely used in daily life, transportation, industrial agriculture, medical and other fields. When using natural rubber to produce all kinds of rubber products, plastic mixing is an important production process. What problems should be paid attention to when using natural rubber?
1. Characteristics of natural rubber molding process
Good plasticizing effect can be obtained by mixing natural rubber in open mixer and internal mixer. When the natural rubber is molded in the open mill, it is recommended to use the low temperature thin pass molding method and the segmented molding method to achieve better molding effect. When the natural rubber 2SLYY228 is molded in the internal mixer, the internal mixing temperature is recommended to be controlled below 155 ℃ for about 13 minutes. When molding natural rubber, do not over refine it, otherwise the high plasticity will cause the physical and mechanical properties of the rubber to decline.
Accelerator M can be used as a plasticizing agent to improve the plasticizing effect of natural rubber in both open mixer and internal mixer. It is recommended that the refined natural rubber be stored for 4-8h before being used in the next process, so that the rubber molecular chain can be relaxed and the plasticity can be uniform.
2. Natural rubber mixing process characteristics
Natural rubber has good mixing performance, which can be mixed by open mixer or internal mixer; The roll wrapping performance is good, the plasticity increases quickly and the heat generation is low during mechanical kneading, so the wetting property of the compounding agent is good, the powder is fast, the dispersion is easy, the mixing time is short, and the mixing operation is easy to master.
When the natural rubber is mixed in the open mixer, the roller temperature of the open mixer is generally controlled at 50-60 ℃, the liquid softener is added after the filler, and the mixing time is among 20-30min. When natural rubber is mixed in an internal mixer, it is recommended to adopt the one-stage mixing method. The discharge temperature is generally controlled at about 140 ℃, and the maximum temperature is not more than 170 ℃. If the mixing time of natural rubber is too long, it will lead to excessive mixing, and the performance of vulcanizate will be significantly reduced. If it is serious, it will cause roller sticking. It is necessary to strictly control the mixing time and other process conditions.
With the continuous progress of the production process of recycled rubber, more and more recycled rubber is used in rubber products with natural rubber as the main raw material. Under the premise of ensuring the quality of products, the cost of raw materials is effectively reduced, especially natural latex recycled rubber and tire recycled rubber. When using natural rubber/recycled rubber to produce rubber products, the process of plastic mixing is slightly different from that of pure natural rubber. Later, the editor will continue to share with you the key points of natural rubber/recycled rubber mixing process.
Exclusive original article [commercial authorization] reprint, excerpt and excerpt in any form are prohibited without written authorization. Focus on Hongyun rubber: learn the process formula and raw material technology of producing rubber products from recycled rubber to help you reduce costs and increase profits