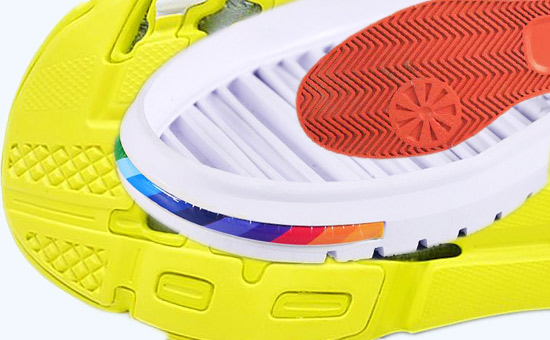
Latex reclaimed rubber can replace natural rubber to produce natural rubber products in whole or in part, which can reduce the cost. Among them, white latex reclaimed rubber has white color and easy color matching, which can replace natural rubber to produce colored rubber products. Colored rubber soles are typical representatives. When using white latex reclaimed rubber to produce colored rubber soles, rubber manufacturers can choose to use a small amount of natural rubber in the formulation to further improve the sole performance while reducing costs1JLYY813 .
1. White pure latex reclaimed rubber and natural rubber are used together to produce colored rubber sole formula
100 parts of white latex reclaimed rubber, 15 parts of natural rubber, 10 parts of white carbon black, 60 parts of light calcium, 3 parts of paraffin, 7.5 parts of white oil, 3.75 parts of zinc oxide, 1.9 parts of stearic acid, and M 1 part of accelerator Agent DM 0.6 parts, accelerator TMTD 0.4 parts, anti-aging agent 4010 1.5 parts, sulfur 2 parts.
2.100% white latex reclaimed rubber and natural rubber are used together to produce colored rubber sole formula
100% white latex reclaimed rubber 100 parts, natural rubber 30 parts, white carbon black 9 parts, light calcium 50 parts, paraffin wax 3.25 parts, white oil 12.5 parts, zinc oxide 4.25 parts, stearic acid 2.25 parts, accelerator M 1.05 parts , Promoter DM 0.5 parts, accelerator TMTD 0.5 parts, anti-aging agent 4010 1.5 parts, sulfur 2 parts.
3. Latex reclaimed rubber / natural rubber color rubber sole color masterbatch dosage
Color masterbatch is a new type of polymer material coloring agent commonly used in the rubber products industry. When using white latex reclaimed rubber and a small amount of natural rubber to produce colored rubber soles, the amount of color masterbatch is not certain, generally according to the color requirements of colored rubber soles. Decide.
4. Production process of colored soles by using white latex reclaimed rubber and natural rubber
1 rubber mixing process: white latex reclaimed rubber and a small amount of natural rubber used in the production of colored rubber soles, usually using fully plasticized natural rubber; first white latex reclaimed rubber, natural rubber (after mastication), white carbon black, light calcium , paraffin, white oil, zinc oxide and stearic acid are placed in an internal mixer, and then kneaded at 120 ° C for about 10 minutes; then the remaining sulfur, accelerator, anti-aging agent is opened in the open mill .
2 vulcanization process: white latex reclaimed rubber / natural rubber and vulcanized with rubber, generally vulcanized at 140 ° C for 10-12 minutes, can be fully vulcanized, and will not cause problems such as scorch, sulfur.
When using white latex reclaimed rubber instead of natural rubber to produce rubber soles, it can reduce the cost with a small amount of natural rubber, and can further improve the mechanical strength and comfort of the colored rubber sole. The amount of natural rubber is directly related to the effective rubber hydrocarbon content of white latex reclaimed rubber. The higher the rubber content of white latex reclaimed rubber, the less the natural rubber blending amount is, and the production cost is more favorable under the same index. It is necessary to select the appropriate index of white latex reclaimed rubber according to actual needs, and reasonably determine the proportion of natural rubber.
Exclusive original article [commercial authorization] reprint, excerpt and excerpt in any form are prohibited without written authorization. Focus on Hongyun rubber: learn the process formula and raw material technology of producing rubber products from recycled rubber to help you reduce costs and increase profits