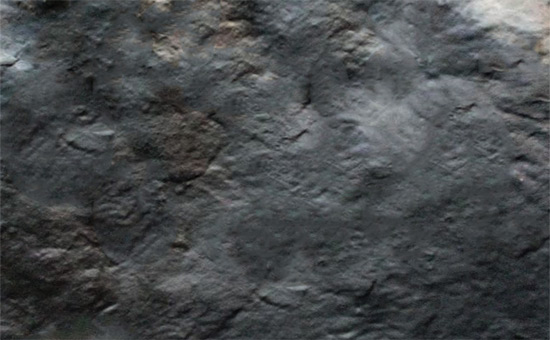
Scorch is the early vulcanization phenomenon caused by heat accumulation in the storage and processing process of rubber materials, resulting in the surface of rubber products is not bright, wrinkled, uneven, and the material becomes brittle and easy to crack. The main reason for coke is the improper selection of the vulcanization system or the unreasonable dosage of vulcanizing agent and accelerator. When using reclaimed rubber as the main raw material to produce rubber products, it is very important to reasonably design the vulcanization system and improve the scorch safety of recycled rubber, especially for recycled rubber products that need to be processed for a long time in the production process.
1. Pay attention to the combination of vulcanizing agent and accelerator of reclaimed rubber
In the vulcanization formula of reclaimed rubber products, choose a vulcanizing agent with a slower reaction speed at the processing temperature, and strictly control the amount of vulcanizing agent to avoid premature scorching caused by excessive use. Preferential use of accelerators with retardant or high critical temperature; Reasonable combination of accelerator and activator (such as zinc oxide, stearic acid, etc.) to achieve the best vulcanization effect and scorching performance.
2. Key points of vulcanization accelerator selection and scorching performance
To improve the coke safety of reclaimed rubber, it is necessary to give priority to the scorch performance of the vulcanization accelerator when selecting the accelerator. It is advisable to choose an accelerator containing an anti-scorch functional group (-SS-) and an auxiliary anti-scorch group (carbonyl, carboxyl, sulfonyl, phosphoryl, thiophosphoryl, benzothiazole). For example, the sulfonamide accelerator E4LYY124 has a long scorching time, fast vulcanization speed, flat vulcanization curve, good comprehensive performance, good processing safety, and is suitable for vulcanization of thick reclaimed rubber products.
The scorch time of each accelerator is increased in the following order: ZDC < TMTD < M < DM < CZ < NS < NOBS < DZ. In practical applications, reclaimed rubber products can be combined with several types of accelerators to achieve the best vulcanization properties and process safety.
3. Accelerator combined to improve the safety of reclaimed rubber scorching
(1) The reclaimed rubber compound formula vulcanized with thiuram accelerator can reduce the amount of thiuram accelerator, and it can be used in combination with sulfenamide or thiazole accelerator to prolong the scorching time.
For example, when TMTD is used as the main accelerator, it can be used in combination with sulfenamide or thiazole accelerator to prolong the scorching time; Avoid using the accelerator TMTD with accelerator D or dithiocarbamate, otherwise it will reduce the scorch resistance of the reclaimed rubber compound.
(2) Guanidine accelerator has high thermal stability, such as accelerator D, as the main accelerator, the rubber coking time is long, and the vulcanization speed is slow.
(3) When natural rubber/reclaimed rubber is used together to produce rubber products, thiazole and hyposulfonamide accelerators can be combined with DTDM to improve the scorch resistance of rubber compounds.
(4) Dithiocarbamate accelerator is selected in the vulcanization system of butyl rubber and butyl reclaimed rubber products, which is more beneficial to the safety of coke. The use of magnesium oxide or accelerator DM in chlorobutyl rubber and chlorobutyl reclaimed rubber containing accelerator TMTD and zinc oxide can prolong the scorching time of the rubber compound.
In the production of reclaimed rubber products, the varieties of vulcanizing agents and accelerators are reasonably selected, and the dosage of them is strictly controlled, which can effectively improve the safety of reclaimed rubber scorching. In actual production, reinforcing agents, fillers, softener varieties, vulcanization conditions of reclaimed rubber will affect the safety of coke, and we will continue to discuss related issues with you in the future.
Exclusive original article [commercial authorization] reprint, excerpt and excerpt in any form are prohibited without written authorization. Focus on Hongyun rubber: learn the process formula and raw material technology of producing rubber products from recycled rubber to help you reduce costs and increase profits