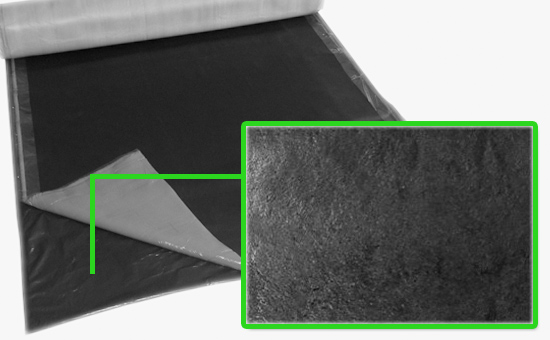
Taking residential buildings as an example, the current residential buildings are higher and higher, and therefore higher requirements are placed on raw materials for the production of waterproofing membranes to avoid cracking problems. Butyl regenerated rubber, like butyl rubber, has excellent water resistance, heat resistance, and aging resistance. The production of waterproofing membranes can reduce raw material costs and maintain good safety performance. So what are the advantages of using waterproof reel produced from butyl reclaimed rubber and how should it be produced?
1. Advantages of butyl reclaimed rubber waterproofing membrane
Butyl reclaimed rubber retains the original performance characteristics of butyl rubber. It has excellent weathering resistance and aging resistance. It can adapt to different environmental changes, especially in ozone-resistant aging and heat-resistant oxygen aging, compared with natural rubber waterproof roll. The anti-ozone performance of the material is more than 10 times better, long-term exposure to the air, the performance change is very small; butyl regenerated rubber itself has good resistance to polar solvents and acids and bases, so the butyl waterproof membrane has excellent anti-corrosion performance Waterproofing membranes have been working “outdoor”. In addition to being exposed to high temperatures and sunlight, they also need to withstand severe cold. The brittle temperature of butyl reclaimed rubber is below minus 40 degrees Celsius. Therefore, butyl regenerated rubber waterproofing membranes have good elasticity and toughness. Tensile strength, basically no embrittlement phenomenon occurs; butyl reclaimed rubber is low in price, plasticity and fluidity are better than butyl rubber. Substituting butyl rubber to produce waterproof membrane can reduce raw material cost and save the cost of electricity and electricity.
2, butyl reclaimed rubber waterproof coil production techniques
When using butyl reclaimed rubber to produce waterproofing membranes, in addition to selecting the appropriate butyl reclaimed rubber product, it is to rationally design the butyl regenerated rubber waterproofing membrane formulation. Under normal circumstances, due to the unsaturation of the butyl regenerated rubber itself. Low, so the amount of sulfur in the vulcanization system should not be too much, the use of thiuram accelerators and thiazole accelerators are used together, and thiuram accelerators can be used as super accelerators to increase the vulcanization speed and uniformity of the thiazole accelerators. In order to increase the activity of organic accelerators, activators in butyl regenerated rubber waterproof coil formulations can use metal oxides such as zinc oxide and some organic acids.
The use of butyl reclaimed rubber to produce waterproofing membranes can reduce production costs and improve the processing technology of butyl waterproofing membranes. It is an ideal new material for waterproofing membranes. At present, more and more manufacturers of waterproof membranes use butyl reclaimed rubber as the main rubber raw material, and some manufacturers will use a small amount of butyl rubber in the butyl reclaimed rubber.
Exclusive original article [commercial authorization] reprint, excerpt and excerpt in any form are prohibited without written authorization. Focus on Hongyun rubber: learn the process formula and raw material technology of producing rubber products from recycled rubber to help you reduce costs and increase profits